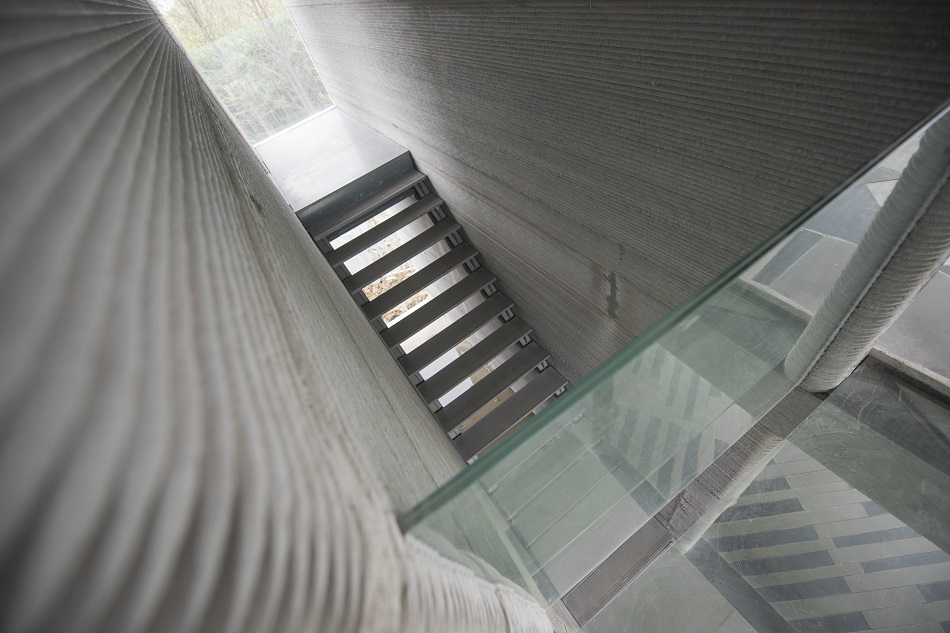
Image Credit: Matjazz/Shutterstock.com
There are currently two main 3D printing technologies in use. Stereolithographic (SLA) printing was developed in the mid-eighties and uses a targeted laser to activate layers in a bath of resin. It is highly recommended for producing high quality, highly detailed models, using an increasingly diverse range of materials and can currently produce models in even glass and metal. However, its limitation is the size of the objects it can create, dictated by the size of the resin bath. It has possibilities as a solution that can supply architectural hardware and items where detail is more important than size but a resin bath that can accommodate a building, or even a section of a building, just doesn’t seem feasible.
Fused Deposition Modelling, or Fused Filament Fabrication, is the most commonly used 3D printing technology and though referred to as FFF or FDM it is essentially the same thing. The system consists of a nozzle that builds a model by depositing layers of material one on top of the other. The nozzle moves in a path determined by the printer software, building the object from the ground up. This approach is scalable, and the size of the nozzle and the framework that supports its movement can be of any size. The material deposited can also be adapted, so rather than a melted polymer that hardens on contact, why not develop concrete that can be used in the same way? That’s exactly the kind of 3D printer that is being used in the construction industry.
Since 2004 when Behrokh Khoshnevis of the University of Southern California's Information Sciences Institute built the first 3D printed wall using a concrete mixture deposited from a gantry-based system, there has been rapid development in the field of 3D printed construction. Currently, there are at least eight companies who can supply 3D construction printers using either a gantry-based approach or a robotic arm with several others at the late development stage.
There are many advantages claimed for constructing buildings using 3D printing technology. The speed of construction is the most obvious: a 3D construction printer works continuously until the job is done. There are also cost savings to be made in terms of reducing wastage of materials and reducing the need for manual labor, though the latter is not necessarily a good thing in countries with high unemployment rates. What it does promise is the potential for flexible, rapidly built low-cost housing using more environmentally sustainable materials than are currently in use.
The materials used in constructing a 3D printed building are as important as the print technology. Whether printing with a robotic arm, gantry, or crane, a conventional concrete could not support its weight as it was being extruded so researchers have looked to develop more appropriate materials in addition to experimenting with faster drying concretes. The University of Nantes, Bouygues Construction, and Lafarge Holcim came together to develop an industrial robot that prints three layers of material at once, essentially creating a sandwich of insulation with a concrete filling. Enrico Dini is the visionary architect behind D-Shape, a printer that is designed to deliver layers of sand or any locally available material, that is then hardened by a binder delivered by the print head. It is this technology that he believes can be used to create structures on the moon using moon-dust and he’s currently working with Sir Norman Foster’s architectural design and engineering firm to make that idea a reality. In 2018, Dutch company MX3D developed a unique construction method called WAAM (Wire Arc Additive Manufacturing) that can 3D print metal structures using a robot equipped with a welder and a nozzle that delivers two kilos of material per hour. It can also work with other metals including stainless steel and bronze.
Arup and CLS Architetti of Italy worked together to produce the first 3D printed concrete house in the EU in only 48 hours, claiming that even using concrete the reduction in waste made the process eco-friendly. The real proof of an eco-friendly 3D construction process came from WASP, a project created by Italian company CSP srl. Their Crane WASP printer used on-site soil mixed with straw, waste rice husk, and lime to complete their GAIA house project that created a minimum environmental impact building. These types of low cost, low impact 3D printed buildings are being trialed to provide a solution to housing shortages in countries as diverse as Brazil and Russia.
So, the 3D construction industry is set to keep on growing with predicted global revenues for the sector of $40bn by 2027. This will be contributed to by Dubai’s mandate for 25% of all their buildings to be 3D printed as part of their construction.
Disclaimer: The views expressed here are those of the author expressed in their private capacity and do not necessarily represent the views of AZoM.com Limited T/A AZoNetwork the owner and operator of this website. This disclaimer forms part of the Terms and conditions of use of this website.