By Samudrapom DamReviewed by Susha Cheriyedath, M.Sc.Updated on Nov 25 2024
Brick recycling breathes new life into old materials, turning bricks from demolition sites into valuable resources. It is a simple yet impactful way to reduce waste and ease the demand for new raw materials.1,2
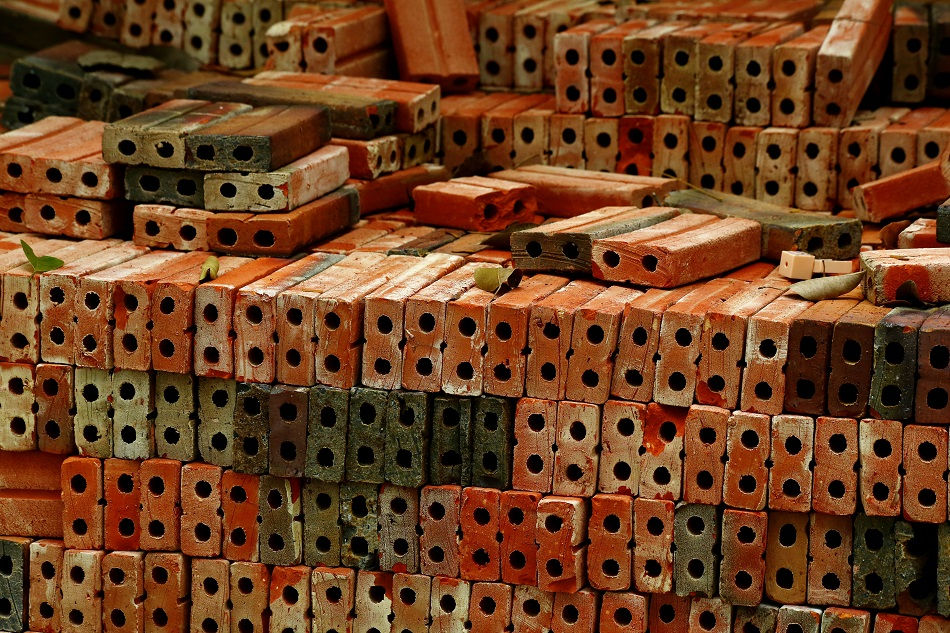
Image Credit: MISS KANITHAR AIUMLA-OR/Shutterstock.com
An Overview of Brick Recycling
Brick recycling is a sustainable process that transforms bricks from demolished buildings, roadways, and other structures into new aggregate materials. Depending on the method used, bricks can be recycled with or without separating the mortar.
Recycling Without Mortar Separation
In this method, the brick and mortar are not separated. Instead, the debris is ground to a maximum grain size of about 0.5 mm, incorporating the mortar into the final product.1 However, the cement content in the mixture plays a crucial role in determining the strength of the recycled bricks. To maintain quality, the mortar content is typically limited to 25 %.
Recycling With Mortar Separation
For this approach, materials in the masonry debris, including mortar, are separated before the brick is reintroduced into the production cycle. The debris is ground to a finer grain size—less than 4 mm—allowing effective removal of mortar and other adhering materials.1 This step is essential for maintaining the visual and structural quality of the recycled bricks, as leftover mortar can cause white spots on the surface due to calcium migration during the firing process.
To achieve thorough separation, various methods are employed, including thermal and mechanical techniques. These processes ensure that the recycled bricks meet the necessary standards for strength and aesthetics.1
Advantages and Challenges of Brick Recycling
Brick recycling offers significant environmental and economic benefits while also facing several challenges. One of the primary advantages is its capacity to reduce construction waste, diverting debris from landfills and contributing to more sustainable waste management practices. By recycling bricks, valuable raw materials like clay are preserved, which reduces the need for extraction and helps conserve natural resources. Additionally, the energy required for recycling bricks is considerably less than that needed to produce new ones from raw materials, leading to lower overall energy consumption. This reduction in energy use not only decreases operational costs but also contributes to a smaller carbon footprint, making brick recycling an environmentally friendly option.
Economically, brick recycling provides substantial cost savings. By utilizing recycled bricks or materials, construction projects can significantly reduce both production and disposal expenses. The growing demand for reclaimed bricks in new construction and restoration projects supports eco-friendly building practices and promotes a circular economy. This shift not only enhances resource efficiency but also aligns with broader sustainability goals within the construction industry.
However, brick recycling does face several challenges that can complicate the process. One major issue is the effective removal of mortar from bricks, which can be time-consuming and technically demanding. Furthermore, masonry debris often contains contaminants such as plastics or metals, making it more difficult to recycle efficiently. The quality of recycled bricks can also be inconsistent; variations in strength and appearance may limit their reuse in construction applications. The economic viability of brick recycling can also be a concern, as the costs associated with labor and processing may sometimes outweigh the benefits of recycling.
Despite these challenges, the advantages of brick recycling are substantial. With ongoing innovations in recycling technologies and a growing awareness of sustainability, many of these issues are likely to be addressed over time. As a result, brick recycling is set to become an increasingly viable and important practice within the construction industry, contributing to both environmental preservation and economic sustainability.1,2,4,5,6
Applications of Recycled Bricks
Recycled bricks have so much to offer in sustainable construction, combining environmental benefits with practical uses. One key area is foundational work—brick aggregates and dust from demolition waste can be used to improve soil stability and strengthen the base of structures. They work well as vertical filter media or for densifying and stabilizing the ground, making them a smart choice for solid and reliable foundations.
Recycled bricks also prove their worth in roadworks. They are commonly used as a material for lean concrete in projects like lintels or low load-bearing structures. Interestingly, lean concrete made from brick waste often turns out stronger than its conventional counterpart. These materials also play a role in low-traffic roads, where they are used as sub-base and base layers, providing a durable and cost-effective solution.
For finishing touches, brick dust is a surprisingly versatile material. When mixed with cement, lime, or natural sand, it creates durable plaster that is perfect for wall surfaces. It is also better at filling voids than traditional materials like sand or stone dust. Recycled brick aggregates, on the other hand, are great for building walls, adding strength and structure without the need for brand-new resources.
Clay brick waste can also be transformed into valuable materials for mortar and concrete. By grinding it down into fine particles, it can replace sand or act as a pozzolanic material to make mixtures denser and stronger. There is even potential to create more advanced materials through processes like alkaline activation. For example, combining brick powder with substances like sodium hydroxide or sodium silicate can create cement with impressive strength and durability, ideal for a variety of construction needs.
Another standout feature of recycled bricks is their durability. Adding brick powder to mortar can make it more resistant to water and sulfate damage, helping structures last longer. In concrete, recycled brick aggregates improve water and air permeability, making the material more resilient and better suited for long-term use.
By embracing recycled bricks, the construction industry is finding new ways to build smarter and more sustainably. These materials not only cut down on waste and conserve resources but also offer innovative, cost-effective solutions for modern building challenges.3,4
How and Why Do We Recycle Concrete?
Recent Advances
Recent studies have highlighted innovative ways to recycle brick waste, offering practical and sustainable solutions for modern construction. These advancements not only reduce waste but also enhance the performance of building materials, demonstrating the versatility of recycled bricks in addressing both environmental and structural challenges.
One study published in the Journal of Sol-Gel Science and Technology proposed an eco-friendly method for turning red brick waste into aerogel panels for thermal insulation. By using waste brick as a precursor, researchers avoided the toxic and costly organosiloxane precursors typically used in aerogel production. The resulting process, which utilized a sol-gel synthesis and ambient pressure drying technique, proved to be faster, more cost-effective, and environmentally sustainable than conventional methods.7
Another study in Heritage and Sustainable Development explored the use of crushed bricks from demolished buildings as additives in concrete. These materials were shown to improve compressive strength and fluidity, enabling the production of lightweight concrete suitable for high-rise buildings and confined spaces. This approach not only repurposes demolition waste but also enhances the usability and performance of concrete in challenging construction environments.8
These advancements demonstrate the growing potential of brick recycling in creating sustainable, high-performance building materials. By repurposing waste bricks into aerogels and concrete additives, researchers are not only reducing landfill waste but also developing products with enhanced properties for modern construction needs.
Conclusion
In conclusion, brick recycling is essential for advancing sustainable construction practices by minimizing waste and conserving natural resources. The process of repurposing bricks for various applications—such as in concrete, road construction, and building foundations—demonstrates its versatility and effectiveness.
Despite the clear environmental and economic advantages, challenges remain, particularly regarding mortar removal and contamination. Addressing these issues is crucial for enhancing the efficiency of brick recycling efforts. Recent innovations, such as utilizing recycled brick waste to create aerogel panels for thermal insulation and incorporating crushed bricks as additives in lightweight concrete, showcase the potential for developing high-performance materials from recycled sources.
These advancements not only improve material properties but also reinforce the importance of integrating recycled materials into the construction industry. By fostering a circular economy, brick recycling contributes significantly to long-term sustainability goals. As research continues and technologies evolve, the prospects for brick recycling will likely expand, further solidifying its role in promoting environmentally responsible building practices.
What to Expect from the Construction Industry by 2030
References and Further Reading
- Balic, M. (2022). Recycling of Bricks. https://epub.technikum-wien.at/obvftwhsmmig/content/titleinfo/9748996/full.pdf
- Fořt, J., Černý, R. (2020). Transition to circular economy in the construction industry: Environmental aspects of waste brick recycling scenarios. Waste Management, 118, 510-520. DOI: 10.1016/j.wasman.2020.09.004, https://www.sciencedirect.com/science/article/abs/pii/S0956053X20305146
- Deb, S., Mazumdar, M., Afre, R. A. (2024). Reuse of Brick Waste in the Construction Industry. Journal of Mines, Metals & Fuels, 72(2). DOI: 10.18311/jmmf/2024/35536, https://www.researchgate.net/publication/380388812_Reuse_of_Brick_Waste_in_the_Construction_Industry
- Zhu, L., Zhu, Z. (2020). Reuse of Clay Brick Waste in Mortar and Concrete. Advances in Materials Science and Engineering, 2020(1), 6326178. DOI: 10.1155/2020/6326178, https://onlinelibrary.wiley.com/doi/full/10.1155/2020/6326178
- Ma, M., Tam, V. W., Le, K. N., & Li, W. (2020). Challenges in current construction and demolition waste recycling: A China study. Waste Management, 118, 610-625. DOI: 10.1016/j.wasman.2020.09.030, https://www.sciencedirect.com/science/article/abs/pii/S0956053X20305419
- Ram, V. G., Prajapati, R. O. H. I. T., Poulose, M. K. (2019). Challenges and prospects of demolition waste recycling in India. Indian Concrete Journal 93(9),75-83. https://www.researchgate.net/publication/364996086_CHALLENGES_AND_PROSPECTS_OF_DEMOLITION_WASTE_RECYCLING_IN_INDIA
- Ait khouya, O., EL farissi, L., Belouaggadia, N., Jammoukh, M., & Zamma, A. (2024). Green recycling of red brick waste into aerogel panels for thermal insulation in buildings. Journal of Sol-Gel Science and Technology, 110(1), 62-73. DOI: 10.1007/s10971-024-06321-z, https://link.springer.com/article/10.1007/s10971-024-06321-z
- Abbas, H. S., Ali, S. S., Hassoon, A. (2023). Using recycled bricks to improve the compressive strength of concrete and produce lightweight concrete. Heritage and Sustainable Development, 5(2), 175-182. DOI: 10.37868/hsd.v5i2.238, https://www.hsd.ardascience.com/index.php/journal/article/view/238
Disclaimer: The views expressed here are those of the author expressed in their private capacity and do not necessarily represent the views of AZoM.com Limited T/A AZoNetwork the owner and operator of this website. This disclaimer forms part of the Terms and conditions of use of this website.