Aug 9 2009
Rockwool, the world's leading manufacturer of non-combustible stone wool insulation, has implemented a new, proprietary production process to reduce the space taken up by a number of its products - providing environmental and cost benefits for itself and its supply chain.
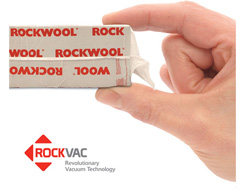
The process, called RockVac, is unique to Rockwool. It involves significant compression of its products and vacuum extraction during their packing.
This means that Rockwool can supply pallets containing a considerably larger volume of some of its products without the need for additional storage space, allowing it to transport more product in fewer vehicles, and taking up less space on site when it is delivered. The compressed products then return to their normal size when the packs are opened.
The RockVac process also helps to retain the products' squarer edges, reducing rounding and curving, thus improving their quality.
Andrew Champ, Marketing Director from Rockwool, said: "RockVac demonstrates our commitment to the development of innovative products and processes. We have invested significantly in our production facility to ensure that RockVac can be implemented across a range of our most popular products. Because we'll now be transporting less air along with our products, we believe RockVac will deliver cost benefits and be kinder to the environment. We also expect our customers will be pleased that fewer vehicles are now needed to deliver product to their sites."
RockVac is now being applied to Rockwool's Cavity, Flexi and RWA45 products. There is no change to the products themselves.