Nov 24 2008
Developers masterminding the UK's biggest steam autoclaving plant at Derwenthaugh EcoParc revealed how the ambitious scheme will take shape today.
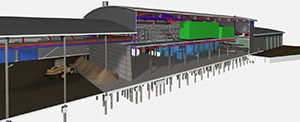
Computer-generated images of the former industrial site show what Graphite Resources’ £50 million deal EcoParc will look like on completion.
The three dimensional design technology created by Virtual Design Services and adopted by Clugston – the main contractor on site, ensured that the steelwork construction fitted to scale. This type of technology has previously been used on aeroplanes such as the Boeing 777. The technology enables users to virtually walk through the site and plan the best places locations for the materials, section by section.
William Thompson, director of Graphite Resources said: "The computer-generated images illustrate where the steam autoclaves will be placed to handle all the waste. The key benefit is that a virtual prototype is built before construction starts. The fact that the design of the EcoParc is 3D leads to significant potential use of the data outside the design and engineering process, proving to be cost and time effective.”
The images show how the steam autoclaving system is housed in a modern, purpose-built facility that uses steam to sterilise and stabilise household, industrial and commercial wastes in a series of large vessels. It will be capable of treating 320,000 tonnes of municipal solid and commercial wastes, and will divert more than 80 per cent of input wastes from landfill.
On completion, the steam autoclaving site will have the capacity to handle waste from 500,000 households.
Richard Greenwood, project manager for Clugston said: “Thanks to the CAD package Archicad 12, users can control their own work and participate in a collaborative review of complex data sources with other team members. The technology means that users can see views previously unavailable to them.
“It's as if a knife had cut through the centre of each image to depict what's happening at the core. People can effectively slice and dice each section to see what’s going on and where everything needs to go. What you see is what you get; you don't have to touch.”
Each autoclave is in essence a long wide steel tube that can handle up to 30 tonnes of waste per cycle. Waste will be fed into each autoclave, either sorted or unsorted and will be evenly distributed throughout each vessel.
All materials will be sterilised at a temperature of up to 160 degrees centigrade. Combined with the rotating action this will ensure that all waste is cleaned and any cellulose material is broken down into fibre flakes known as CellMatt®.
An ultra violet odour treatment will ensure that all bacterial smells are destroyed. At the end of each cycle, the sterilised material will be sent to the screening and segregation plant where it is separated into various materials such as CellMatt®; fibre; glass; plastic; steel; aluminium and other residues.
The Derwenthaugh EcoParc will act as the blueprint for all future sites and comprises four key areas - municipal solid waste/ commercial waste reception; steam treatment and reception; separation plant; light waste, despatch and green waste transfer station. Additional office and floor space will be created for future development. The waste processing buildings will feature the latest UV odour treatment technology and be held at a negative pressure to prevent the release of any odour.
The EcoParc designed by award-winning architects Brown SmithBaker covers the majority of the five acre site.