Aug 12 2008
If wind turbines clatter and whistle too loudly, they are only permitted to operate under partial load to protect the local residents – but this also means a lower electricity output. An active damping system cancels out the noise by producing counter-vibrations.
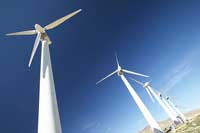
If wind energy converters are located anywhere near a residential area, they must never become too noisy even in high winds. Most such power units try to go easy on their neighbors’ ears, but even the most careful design cannot prevent noise from arising at times: One source is the motion of the rotor blades, another is the cogwheels that produce vibrations in the gearbox. These are relayed to the tower of the wind turbine, where they are emitted across a wide area – and what the residents hear is a humming noise. “People find these monotone sounds particularly unpleasant, rather like the whining of a mosquito,” says André Illgen, a research associate at the Fraunhofer Institute for Machine Tools and Forming Technology IWU in Dresden. If the wind energy converters hum too loudly, they are only permitted to operate under partial load: They rotate at a slower speed and generate less electricity. In some cases the operators have to install additional damping systems or even replace the gearbox – an expensive business. However, the effectiveness of the passive damping systems used until now is somewhat limited: They only absorb noise at a certain frequency. Since modern wind energy converters adapt their rotational speed to the wind velocity in order to generate as much electricity as possible, however, the frequency of the humming sound also varies. Despite noise attenuation measures, humming noises penetrate the surrounding area.
In a joint project with colleagues from Schirmer GmbH, ESM Energie- and Schwingungstechnik Mitsch GmbH and the Dr. Ziegler engineering office, IWU researchers have developed an active damping system for wind turbines. The project is being funded by the “Deutsche Bundesstiftung Umwelt”. “These systems react autonomously to any change in frequency and damp the noise – regardless of how fast the wind generator is turning,” says Illgen. The key components of this system are piezo actuators. These devices convert electric current into mechanical motion and generate “negative vibrations”, or a kind of anti-noise that precisely counteracts the vibrations of the wind turbine and cancels them out. The piezo actuators are mounted on the gearbox bearings that connect the gearbox to the pylon. But how do these piezo actuators adjust themselves to the respective noise frequencies? “We have integrated sensors into the system. They constantly measure the vibrations arising in the gearbox, and pass on the results to the actuator control system,” says Illgen. The researchers have already developed a working model of the active vibration dampers, and their next step will be to perform field trials.