Concrete is a highly utilized material across the world, and regarding human resources, only water surpasses concrete in terms of its level of consumption.
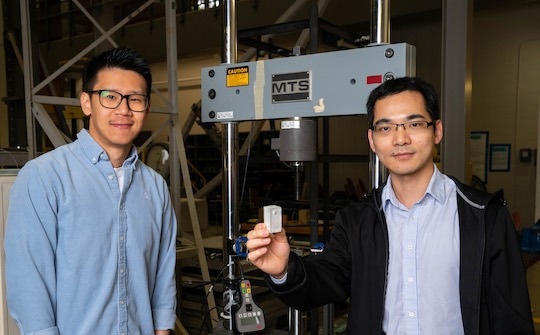
A group of scientists at Rice University in Texas has developed an eco-friendly cement that could lay the foundations for building a greener future.
Image Credit: Gustavo Raskosky/Rice University
The production of cement, a crucial element in making concrete, is responsible for approximately 8% of the world’s carbon dioxide emissions, making the cement industry the third-largest global contributor to greenhouse gas emissions, just behind the United States and China.1
Moreover, according to the International Energy Agency (IEA), the intensity of carbon dioxide (CO2) produced during cement manufacturing increased at an annual rate of roughly 1.5% between 2015 and 2021.1 This is particularly concerning as to achieve the ambitious goal of net zero emissions by 2050, there needs to be a significant reduction in CO2, at an average of 3% per year, until 2030.1 Therefore, finding greener materials or ways of manufacturing cement for use in concrete is crucial.
Now, a group of scientists at Rice University has developed an eco-friendly cement that could lay the foundations for building a greener future.
The Flash Joule Heating Process
Traditionally, fossil fuels, such as coal, natural gas, and petroleum, are used in the cement-making process. However, these substances emit significant greenhouse gases as they require extremely high temperatures within the cement production process to purify the mixture.
In the hope of helping to meet the Net Zero goals, the team at Rice University experimented with flash joule heating, using it to remove toxic heavy metals from fly ash – a component typically used in concrete production.
Upon investigation, the team found that using this purified fly ash in concrete production improved the final product's overall quality and reduced the amount of cement needed.
You can use less concrete if you use coal fly ash. However, fly ash contains heavy metals... Often, we try to fix one thing and we mess something else up. In our effort to do something with this waste, namely coal fly ash, we were polluting our environment because the heavy metals were leaching out. Water carried it into our environment and contaminated our soil along roadways, etc.
Prof. James Tour, Professor of Materials Science & NanoEngineering, Rice University
Improved Strength and Elasticity
The focus of the study was to make cement production more environmentally compatible.
Reducing emissions from cement production is very important to mitigate global greenhouse emissions… This is the big picture of this study
Bing Deng, Tour Lab, Rice University
The team was able to demonstrate significant decreases in CO2 and heavy metal emissions by 30% and 41%, respectively.1 As an added, unexpected bonus, the method was also found to improve the strength and elasticity of concrete.
By using this method, we can eliminate the heavy metals from coal fly ash with very high efficiency… For different heavy metals like arsenic, cadmium, cobalt, nickel and lead, the removal efficiency is up to 70% to 90% in just one second. This is a very rapid discharging process.
Bing Deng, Tour Lab, Rice University
The process established by the team at Rice University collected the evaporated heavy metals in a vacuum chamber rather than releasing them back into the environment. Additionally, the energy consumption of the process proved to be relatively low.
It’s a big win for the environment… You’re reducing emissions, and you’re not leaching heavy metals in the process.
James Tour, Rice University
Thus, the team has successfully shown that it is possible to develop more environmentally friendly concrete without compromising on vital qualities such as strength and durability.
References and Further Reading
-
Clark, S.C. (2023) Eco-efficient cement could pave the way to a Greener Future, Rice News | News and Media Relations | Rice University. Available at: https://news.rice.edu/news/2023/eco-efficient-cement-could-pave-way-greener-future
-
Deng, B. et al. (2023) “Heavy metal removal from coal fly ash for low carbon footprint cement,” Communications Engineering, 2(1). Available at: https://doi.org/10.1038/s44172-023-00062-7
Disclaimer: The views expressed here are those of the author expressed in their private capacity and do not necessarily represent the views of AZoM.com Limited T/A AZoNetwork the owner and operator of this website. This disclaimer forms part of the Terms and conditions of use of this website.