By Nidhi DhullReviewed by Susha Cheriyedath, M.Sc.Aug 8 2024
The global construction sector is responsible for a substantial share of energy consumption and energy-related CO2 emissions. Moreover, traditional construction methods that rely on cement, concrete, and masonry are increasingly seen as outdated, lacking in innovation, efficiency, and sustainability. Cold-formed steel (CFS), as a modern construction method and alternative material, offers a promising solution to mitigate these environmental impacts. By incorporating CFS, the industry can move towards more sustainable practices, reducing its carbon footprint while enhancing efficiency and innovation in construction processes.1,2
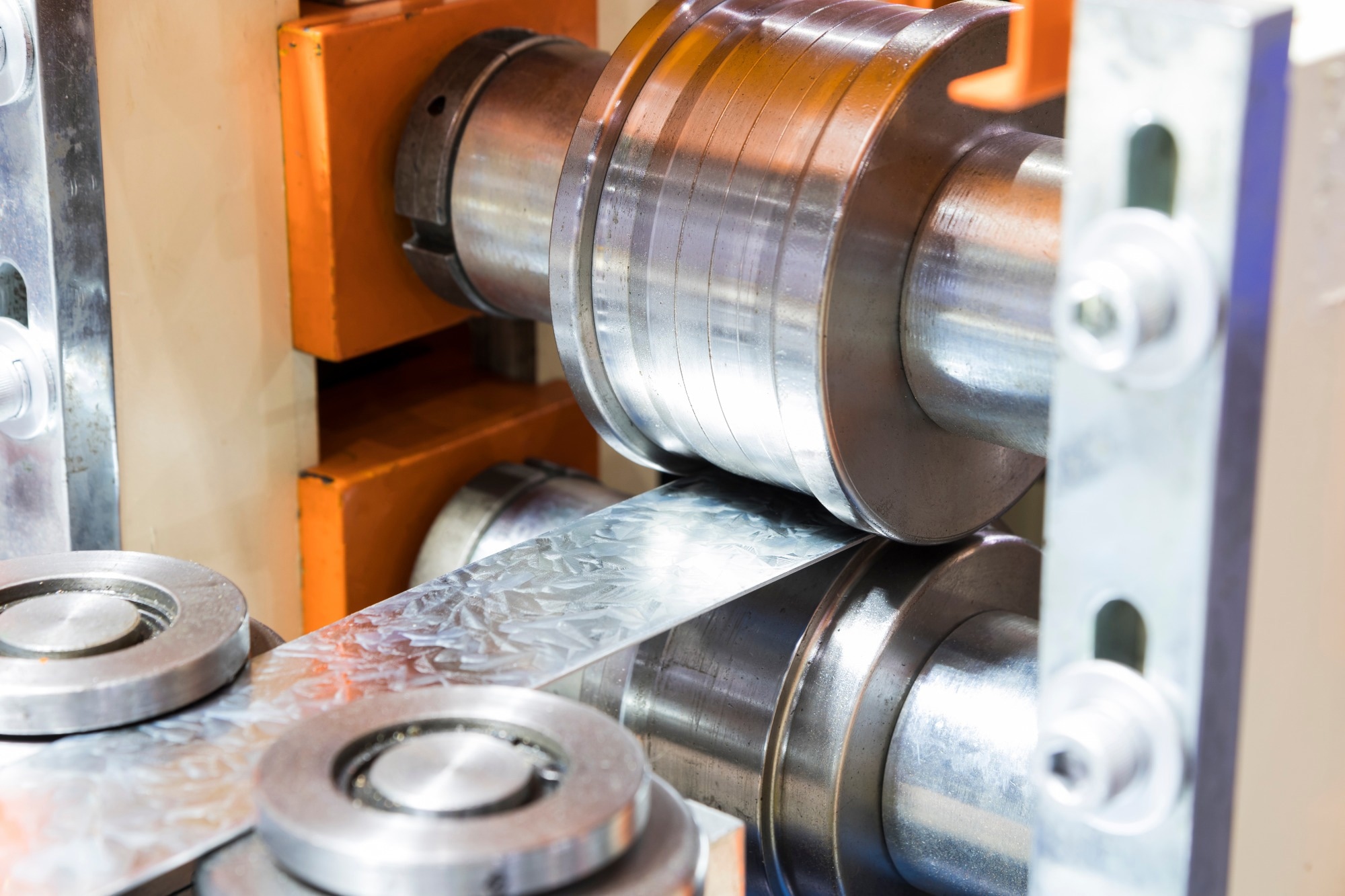
Image Credit: Mr.1/Shutterstock.com
CFS structures offer numerous advantages in construction such as excellent strength-to-weight ratio, recyclability, and reusability. CFS can be rolled into diverse cross-sectional shapes and optimized to enhance their load-bearing capacities for economical and efficient building solutions.1 High thermal insulation and low operational energy consumption are added advantages of CFS structures.2 Thus, this article explores various CFS designs and their application and advantages in construction.
Designing CFS Structures
CFS elements are rolled from thin gauge steel sheets into desired shapes using a forming machine at ambient temperature.1 High-strength steel such as G550 is generally used to prepare these CFS elements, with thicknesses ranging between 0.01 mm to 7 mm depending on their structural or non-structural usage.2
Thinner CFS sections sections, while being highly stiff, are also susceptible to local and distortional buckling. To counteract this, complex shapes featuring multiple segments, stiffeners, and lipped channels are designed to enhance their buckling resistance. These CFS sections are then combined to create various cross-sectional geometries. For example, two identical lipped channel sections can be connected face-to-face to form a box section or back-to-back to create an I-section. These built-up CFS sections can be further expanded and modified to achieve greater compression and bending capacities, making them versatile and efficient in structural applications.1
CFS is typically utilized in buildings through three primary construction methods: stick-built construction, panelized modules, and volumetric modules. In stick-built construction, individual prefabricated CFS elements are transported to the construction site and assembled on-site into the desired structure. In contrast, panelized and volumetric modules are prefabricated in a controlled factory environment and then transported to the construction site as partially or fully completed units, offering increased efficiency and quality control.2
To ensure the structural integrity and performance of CFS structures, different design codes have been developed, with the most common being the North American or American Iron and Steel Institute (AISI) Specification, the Australian/New Zealand Standard (AZ/NZS), and the Eurocode. These codes outline two primary design methods to predict the axial strength of columns and the flexural capacity of beams: the effective width method (EWM) and the direct strength method (DSM). The DSM, being the newer and simpler of the two, is increasingly favored in modern design practices.1
To prevent corrosion in CFS structures, various coating methods are employed, including anodizing, galvanizing, powder coating, painting, epoxy coating, and duplex coating. Among these, galvanization with zinc is the most commonly used method due to its effectiveness and cost-efficiency in protecting the steel from corrosion.2
Applications and Advantages in Construction
CFS has become an increasingly popular choice in the construction industry, and for good reason. Its lightweight yet strong nature, along with its ability to be mass-produced, makes it incredibly versatile both in factory settings and on construction sites.2 One of the biggest advantages of steel is that it is nearly 100 % recyclable, which means that using CFS helps reduce construction waste significantly. Unlike other materials, like wood, recycled steel does not lose any of its quality or strength. It remains just as durable and reliable as the original, making it an excellent choice for sustainable construction.1
CFS is widely used in buildings for both primary and secondary structural components because it offers high load-bearing capacity, flexibility in design, and stability.3 You will often see it being used in roofs, walls, storage racks, and other supporting structures. Its popularity has surged in modular construction, where it has been seen as a modern alternative to traditional on-site building methods.1
Another big plus for CFS is its low maintenance needs.1 Steel does not suffer from moisture damage or biological decay, so it lasts a long time with minimal upkeep. In fact, CFS elements in walls or floors can last over 200 years, even in challenging environments.2
When it comes to energy efficiency, CFS structures have a lot to offer. Since the operation phase of a building’s lifecycle accounts for the majority of its energy use—especially for heating and cooling—CFS can help create more energy-efficient buildings. Its design allows for better thermal performance, reducing heat loss and improving insulation, which can lead to lower energy bills. Plus, steel frames can enhance sound insulation, making buildings quieter and more comfortable.1
The rise of advanced manufacturing techniques, powerful simulation tools, and innovative design methods have further accelerated the use of CFS. These developments have expanded its application beyond just traditional buildings, making it a go-to material for mid-rise apartments, multi-family homes, and even larger civil structures like bridges and towers. With its many benefits, CFS is proving to be a key player in the future of sustainable construction.3
Challenges and Solutions
Despite the numerous advantages of CFS, there are some challenges that limit its broader application in construction. One of the primary concerns is its thermal behavior. Steel's high thermal conductivity can lead to significant heat loss or gain through a phenomenon known as thermal bridging. This can negatively impact the thermal performance and energy efficiency of buildings. Therefore, it is crucial to carefully optimize the design of CFS structures to address these issues. This can be achieved by focusing on energy dissipation, improving structural capacity, and balancing material costs.1
Another challenge with CFS is its susceptibility to buckling instabilities due to its limited thickness. Even at stress levels below the yield strength, CFS elements can experience buckling, which restricts their use in primary structures, especially in taller buildings. However, innovations such as hollow flange sections, which lack free edges, can help mitigate buckling issues. To ensure the safe and effective use of CFS, designs must consider factors such as allowable stress, load and resistance, and other structural specifications. This also underscores the importance of rigorous quality control during both the manufacturing and construction phases.3
In advanced construction applications, CFS structures are becoming increasingly sophisticated and complex. Traditionally, the mechanical properties of these elements have been studied using destructive tensile tests. However, non-destructive methods, such as 3MA (micromagnetic multiparameter microstructure and stress analysis) techniques, offer a faster and more efficient way to reveal important material characteristics like yield strength, tensile strength, and residual stress distribution. These insights can significantly enhance the optimization of CFS structures.
By incorporating neural networks, genetic algorithms, and trust region methods, engineers can improve the load-bearing capacity, energy efficiency, and fire performance of CFS, making it a more viable option for a wider range of construction projects.3
Latest Developments
Researchers are making considerable strides in using innovative technologies to improve the practical application of CFS elements. For example, a recent study published in Thin-Walled Structures explored the use of machine learning (ML) to predict and optimize the fire resistance time (FRT) of CFS walls. ML offers a way to address the high costs and lengthy processes associated with traditional full-scale experiments and numerical studies. In this study, researchers used the XGBoost (eXtreme Gradient Boosting) model, training and testing it with various wall configurations and types of sheathing boards. The model was impressively accurate, predicting the FRT of CFS walls with a mean absolute error of just 8.46 %.4
Another recent study in the International Journal of Engineering Trends and Applications examined an industrial roof truss with and without a CFS section. CFS could effectively withstand ions, seismic loads, and unbalanced forces, exhibiting significantly less deflection. Moreover, using CFS reduced the total costs of truss installation by 14 % compared to conventional composite beams and bridge girders. However, the SFS section’s ductility was insufficient, requiring further investigation.5
In conclusion, optimizing CFS elements for improved load-bearing capacity, energy efficiency, and thermal performance can lead to reliable and cost-effective building solutions. This can be achieved through the use of advanced optimization algorithms and the development of innovative designs.
References and Further Reading
1. Liang, H., Roy, K., Fang, Z., & Lim, J. B. P. (2022). A Critical Review on Optimization of Cold-Formed Steel Members for Better Structural and Thermal Performances. Buildings, 12(1), 34. DOI: 10.3390/buildings12010034, https://www.mdpi.com/2075-5309/12/1/34
2. Tharmarajah, G., & Doren, K. V. (2023). Cold Formed Steel for Residential Construction – Design Philosophy and Durability Assessment. Preprints, 2023090106. DOI: 10.20944/preprints202309.0106.v1, https://www.preprints.org/manuscript/202309.0106/v1
3. Poologanathan, K., Perampalam, G., Gunalan, S., & Corradi, M. (2023). Structural Performance of Cold-Formed Steel (CFS) Structures. Buildings, 13(7), 1689. DOI: 10.3390/buildings13071689, https://www.mdpi.com/2075-5309/13/7/1689
4. Liu, K., Yu, M., Liu, Y., Chen, W., Fang, Z., & Lim, J. B. P. (2024). Fire resistance time prediction and optimization of cold-formed steel walls based on machine learning. Thin-Walled Structures, 112207. DOI: 10.1016/j.tws.2024.112207, https://www.sciencedirect.com/science/article/abs/pii/S0263823124006499
5. Raghav, G. S., & Khan, M. (2024). A Review of An Examination of Industrial Roof Truss with Or Without Cold Formed Steel Section. International Journal of Engineering Trends and Applications (IJETA), 11. DOI: 10.33144/23939516/IJETA-V11I1P1, https://www.ijetajournal.org/volume-11/issue-1/IJETA-V11I1P1.pdf
Disclaimer: The views expressed here are those of the author expressed in their private capacity and do not necessarily represent the views of AZoM.com Limited T/A AZoNetwork the owner and operator of this website. This disclaimer forms part of the Terms and conditions of use of this website.