By Nidhi DhullReviewed by Susha Cheriyedath, M.Sc.Aug 1 2024
The construction industry is increasingly embracing innovative technologies to enhance its processes. One such technology is laser scanning, which is widely used to capture and process data related to assets and construction projects.1 Laser scanning is a reality capture technique that creates detailed three-dimensional (3D) models representing the current state of buildings. This process involves generating 3D point clouds of both indoor and outdoor environments from laser scanning data.2
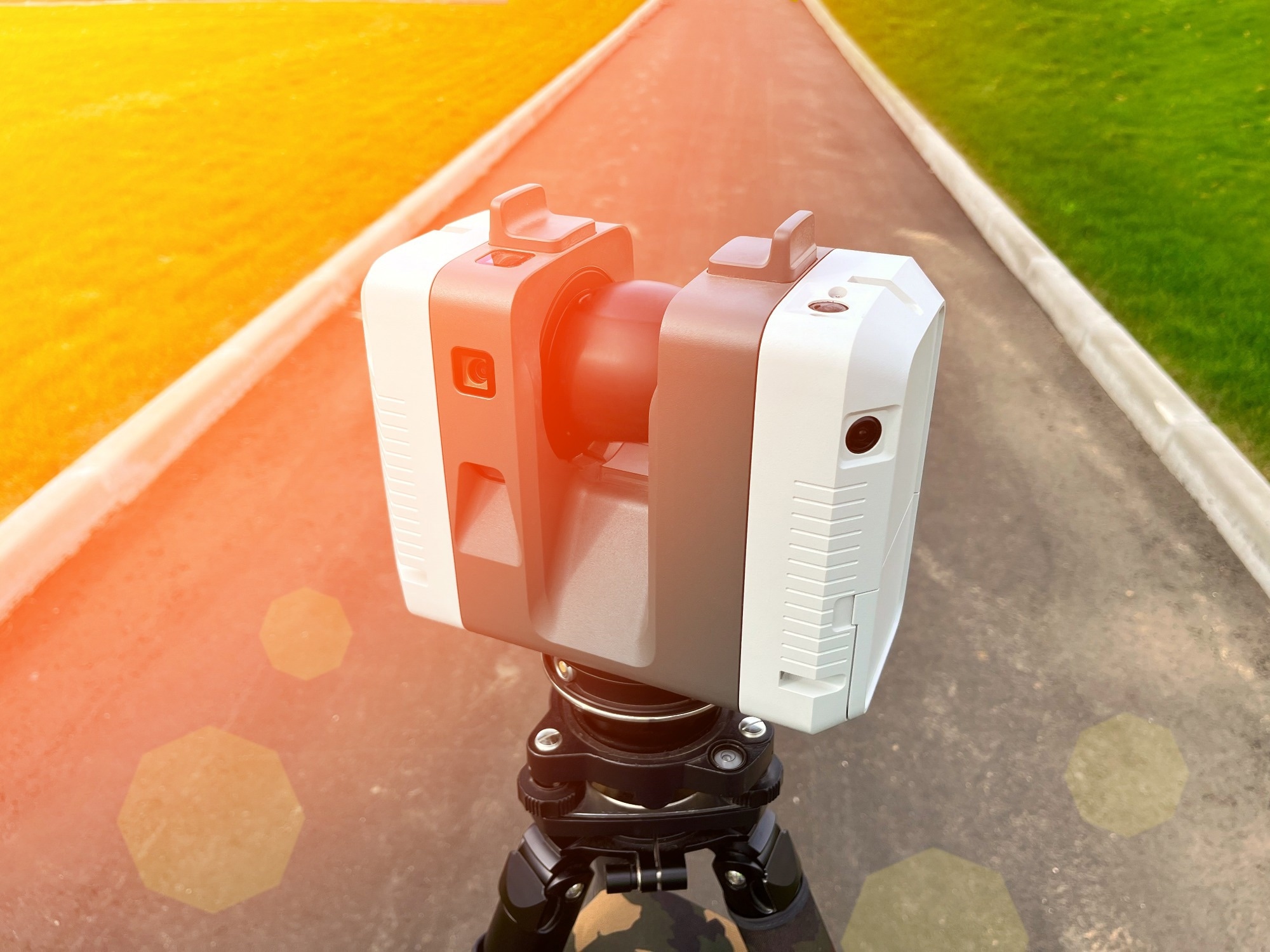
Image Credit: AntonSAN/Shutterstock.com
Real data capturing through laser scanning finds numerous applications in construction, including progress monitoring, rehabilitation, facility maintenance, and waste management.1,2 This article explores different laser scanning technologies, their application in enhancing precision and reducing rework in the construction sector, and existing challenges.
Laser Scanning Technologies
Laser scanning, called high-definition surveying or reality capture, uses a laser to accurately map an area of interest. It captures detailed data on a construction site, providing accurate information for all project stages. Construction professionals infer this recorded data as a point cloud, a database connecting points in a 3D coordinate system. This highly accurate digital record of an object or space comprises raw information that can be processed to extract useful information for the target applications.1
Laser scanning techniques are broadly classified based on different working platforms: terrestrial (TLS), airborne (ALS), and mobile (MLS). While TLS is a ground-based method with a laser usually mounted on a static tripod, the scanning system is mounted on an aircraft such as an unmanned aerial vehicle (UAV) or helicopter.3
Alternatively, MLS used land-based mobile platforms such as cars or robots. All these systems differ in scanning mechanism, speed, and accuracy. For instance, ALS and MLS can quickly scan large areas and areas with limited accessibility, while TLS provides more detailed point clouds with relatively high accuracy and low cost.3
The overall performance of a laser scanner depends on numerous factors, including angular resolution, scanning speed, and required range. In addition, the quality of the point clouds generally depends on the number of times the measurement is repeated for each point; a higher number of measurements per point yields better-quality point clouds.2
Using 3D Laser Scanners for Additively Manufactured Product Quality Control
Application in Construction
Laser scanning is versatile and finds applications across various construction processes, including surveying, component manufacturing, construction monitoring, maintenance, and the restoration of heritage buildings. This technology consolidates the collection, documentation, and analysis of 3D data for as-built buildings and infrastructure when integrated with other construction technologies.1
Information on material and color retrieved from point clouds helps identify the topology of building elements. Data on texture, intensity, and RGB color space reveals spatial relationships between structures and their surface properties, facilitating the identification of walls, floors, ceilings, and openings like doorways and windows.1
Laser scanning is often integrated with other construction technologies to enhance its functionality. For example, when combined with Building Information Modeling (BIM), it supports monitoring, cost estimation, quality assessment, 3D visualization, and spatial analysis, leading to improved building accuracy and reduced errors and rework. Additionally, the scan-to-BIM approach is gaining popularity for enhancing construction management and maintenance by providing real-time as-built information.3
Beyond capturing as-built components, laser scanning is also applied to the reconstruction of civil structures such as bridges, tunnels, prefabricated concrete elements, bridge piers, and movable floodwalls. Furthermore, integrating laser scanners with ground-penetrating radar allows for detailed internal geometry analysis of structures like tunnels and bridges.3
Advantages
Laser scanning provides numerous advantages that enhance precision and reduce rework in the construction sector. One of its key benefits is the significant reduction in survey duration, with scanners acquiring over a million points per second, which boosts productivity. The high-density sampling capability of laser scanners enables rapid and accurate collection of data that faithfully represents complex geometries.3
In addition to 3D positional information, laser scanners capture data such as reflected intensity values and RGB colors. This comprehensive data collection supports precise modeling of dimensions, spatial positioning, and structural details. The high level of automation in laser scanners also makes them user-friendly, allowing operators to conduct surveys effectively without requiring specialized technical skills.1,3
Moreover, since most objects can reflect laser beams, the scanning process is non-contact, ensuring the safety of the equipment in hazardous environments and minimizing disruption to the construction process. The increased density of point clouds generated further enhances the accuracy of models produced through laser scanning.3
Challenges
Despite the proven efficiency of laser scanning in accurately capturing built environments, its adoption in the construction industry is still limited due to technical challenges and knowledge gaps. For instance, while increasing productivity in construction could potentially save up to USD 1.6 trillion, many construction professionals remain hesitant to adopt these technologies. This reluctance is often due to limited understanding and the absence of a comprehensive support framework.1
Technically, laser scanning systems face issues related to portability and site constraints. Additionally, while insufficient data can render a model unusable, collecting excessive amounts of data can be time-consuming and result in redundant information.1
Laser scanners capture all physical objects within their field of view, including unwanted items. The resulting massive point clouds from these extraneous objects can complicate model generation and point cloud production. To address this, additional processing steps such as de-noising are required to create a clear and accurate model.1
Furthermore, high costs associated with both hardware and software pose significant barriers to broader adoption. The expense of laser scanning technology can be prohibitive, even for smaller projects or those not requiring high precision. Additionally, data processing applications currently struggle to meet the demands for efficiency, effectiveness, and automation, further impeding widespread use.3
Advances in 3D Imaging for Urban Building Monitoring
Latest Developments & Future Prospects
Significant efforts are being made to overcome the existing challenges and increase the application of laser scanners in the construction industry. For instance, a recent study in Automation in Construction demonstrated using a combination of TLS and UAV-based obliques photography in bridge construction. A convenient UAV flight planning approach and an efficient framework for automatically extracting bridge alignment from point cloud data were proposed. This optimized system was effectively applied to an under-construction long multi-span girder bridge.4
Another recent study in Structural Control & Health Monitoring employed 3D laser scanning for deformation monitoring of a tunnel based on the new Austrian tunneling method (NATM). The Kriging filtering algorithm was proposed to improve the accuracy of laser scanning technology and estimate the real-time deformation of NATM tunnel excavation from point clouds. The successful application of such systems can help realize effective safety warnings for tunnel construction.5
In conclusion, combining laser scanning with other advanced remote sensing technologies and processing methods such as artificial intelligence and deep learning can help acquire reliable on-site data accurately and timely.
References and Further Reading
1. Almukhtar, A., Saeed, Z. O., Abanda, H., & Tah, J. H. M. (2021). Reality Capture of Buildings Using 3D Laser Scanners. CivilEng, 2(1), 214–235. DOI: 10.3390/civileng2010012, https://www.mdpi.com/2673-4109/2/1/12
2. Moselhi, O., Bardareh, H., & Zhu, Z. (2020). Automated Data Acquisition in Construction with Remote Sensing Technologies. Applied Sciences, 10(8), 2846. DOI: 10.3390/app10082846, https://www.mdpi.com/2076-3417/10/8/2846
3. Wu, C., Yuan, Y., Tang, Y., & Tian, B. (2021). Application of Terrestrial Laser Scanning (TLS) in the Architecture, Engineering and Construction (AEC) Industry. Sensors, 22(1), 265. DOI: 10.3390/s22010265, https://www.mdpi.com/1424-8220/22/1/265
4. Han, Y., Feng, D., Wu, W., Yu, X., Wu, G., & Liu, J. (2023). Geometric shape measurement and its application in bridge construction based on UAV and terrestrial laser scanner. Automation in Construction, 151, 104880. DOI: 10.1016/j.autcon.2023.104880, https://www.sciencedirect.com/science/article/abs/pii/S0926580523001401
5. Hu, D., Li, Y., Yang, X., Liang, X., Zhang, K., & Liang, X. (2023). Experiment and Application of NATM Tunnel Deformation Monitoring Based on 3D Laser Scanning. Structural Control & Health Monitoring, 2023, 1–13. DOI: 10.1155/2023/3341788, https://onlinelibrary.wiley.com/doi/full/10.1155/2023/3341788
Disclaimer: The views expressed here are those of the author expressed in their private capacity and do not necessarily represent the views of AZoM.com Limited T/A AZoNetwork the owner and operator of this website. This disclaimer forms part of the Terms and conditions of use of this website.