The use of plastics for construction has become a major environmental concern. Reducing reliance on plastics and replacing them with sustainable construction materials can lead to a greener future. This article explores the use of plastics in construction and the shift towards alternative eco-friendly materials.
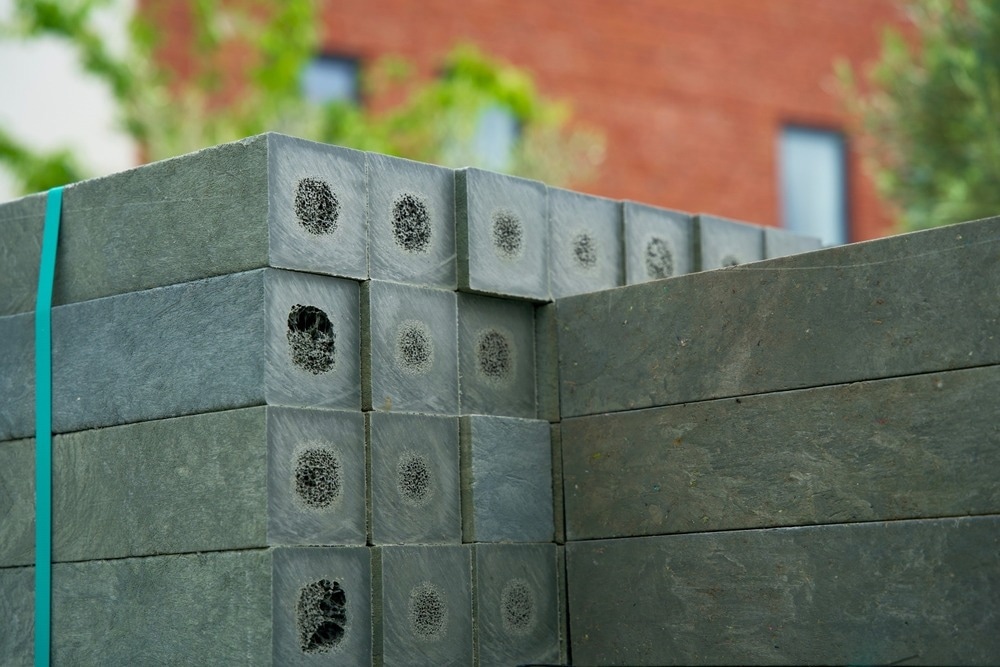
Image Credit: Rene Notenbomer/Shutterstock.com
Plastic in Construction
The increasing amount of plastic waste in ecosystems can be effectively addressed through recycling and reuse. One approach that has gained significant attention is the use of plastic waste as a component of construction materials.
Plastics commonly used in construction include polyvinyl chloride (PVC), expanded polystyrene (EPS), and high-density polyethylene (HDPE), which are employed to build seals, pipes, windows, doors, floor coverings, cables, insulation, and packaging.
Concrete is a commonly used construction material that provides better fire resistance than other building materials. Conventionally, concrete is composed of coarse and fine aggregates, cement, and water. Although concrete can withstand higher compression, the absence of an appropriate preconditioner may lead to numerous weaknesses and flaws owing to its low tensile strength.
Hence, concrete is mixed with 65–85% aggregates to impart strength. To this end, partially replacing aggregates with plastic waste in concrete mix preparation will provide an alternative solution for utilizing plastics in construction.
The two forms of plastic waste used in building materials are plastic aggregates and fibers. Plastic aggregates are employed to replace coarse and fine aggregates because of their lower bulk density, which makes them preferable to granite, limestone, and basalt.
Steel fibers are used to improve the mechanical and strength durability of concrete and are susceptible to corrosion when exposed to marine or saline water. Hence, reinforcing concrete with plastic fibers can help combat such problems.
Three-Dimensional (3D) Printing of Plastics in Construction
3D printing technology offers designers greater flexibility in creating complex frameworks. A new approach for utilizing plastic waste in the construction industry has emerged by incorporating plastic waste into 3D concrete printing.
3D printing is a rapid, safe, and cost-effective construction process. These devices operate without interruptions, thus ensuring high efficiency. Adopting 3D printing in residential buildings is more cost-effective than the traditional methods, which can significantly lower the cost of apartments.
Although 3D printing technology may not entirely replace conventional building methods, it can offer significant support, particularly for creating components with intricate and complex geometries. To achieve high-quality printing, it is crucial to use appropriate building materials with the required technical properties.
3D printing of plastic-based construction components offers a promising solution to the global problem of repurposing plastics in construction. Despite their potential, the application of 3D printing in civil engineering is currently undervalued. If well-adopted in the industry, 3D-printed plastic components have the potential to revolutionize the construction process and can be utilized to create innovative frameworks or unconventional reinforcements.
Bioplastic as a Substitute for Plastic in Construction Industry
Bioplastics are used in concrete blends and dry premixed mortars as additives in the construction industry. Bio-based aggregates have more advantages than their synthetic equivalents. Bio-based additives are primarily used in concrete mixtures, paints, mortars, exterior and interior coatings, stucco, gypsum boards, and joint mortars.
Organic admixtures such as protein hydrolysates, lignosulfonates, and welan rubber are commonly added to concrete mixtures for various reasons. Lignosulfonates are widely used as admixtures to improve the fluidity and workability of concrete, resulting in increased plasticity and reduced water content. This leads to enhanced mechanical properties and durability.
Precast concrete employs lignosulfonates to enhance its mechanical strength, whereas protein hydrolysates are used to significantly decrease the surface tension of water during the production of expanded concrete.
Protein hydrolysates create spherical foam bubbles that offer approximately 20% higher compressive strength than the synthetic foam-generated hexagonal bubbles. Protein hydrolysates are preferred in situations in which low-specific-gravity foam concrete must be created while maintaining its compressive strength.
A biopolymer is used as an additive in a hydraulic lime mortar to achieve positive effects on its mechanical properties owing to the adhesive nature of the material. Among natural polymers, cactus extract is an interesting alternative to plastic because of its ability to improve both the mechanical strength and durability of hydraulic lime mortar in an eco-friendly manner.
Recent Studies
A study published in Civil and Environmental Engineering examined the influence of plastic/glass powder on the physical and mechanical properties of fired clay bricks. The study utilized fired clay bricks made with different plastic/glass content ratios (00/20, 05/15, 10/10, 15/05, and 20/00 by weight) as a substitute for clay while keeping the soil-to-water ratio constant.
The bricks were subjected to three firing phases, with maximum temperatures of 300, 600, and 900°C for the first, second, and third phases, respectively. The results revealed that the water absorption and efflorescence of the clay brick samples increased, but the density and firing shrinkage decreased with an increase in plastic quantity.
In contrast, increasing the glass powder content in clay brick samples resulted in a decrease in water absorption and efflorescence. Overall, clay brick samples with a higher plastic powder content showed improved mechanical properties compared to those with glass powder.
Another study published in Sustainability examined the noise-reducing properties of resonators created from synthetic cord fiber and plastic using 3D printing technology. The absorption and insulation properties of the fabricated structures were tested with an interferometer.
The results showed that a 100 mm long resonator (X or O shaped) design with a 2.0 mm perforation, 20 mm thick plate achieved a good sound absorption peak at 315 Hz of 0.94. In contrast, the 50 mm long resonator (X- or O-shaped) with the same perforation size and plate thickness showed a better sound absorption peak at 500 Hz of 0.95.
The results showed that the combined plastic and rubber structures can be integrated into building structures to improve building acoustics and reduce noise and reverberation.
Conclusion
Plastics have become a ubiquitous part of the construction industry due to their numerous advantages, but their ecological impact is significant, leading to pollution and long-lasting damage to the environment. To mitigate these negative consequences, it is essential to explore alternative materials, advanced technologies, and sustainable practices for recycling and reusing plastic waste and even replacing it with more environmentally friendly materials altogether. This will pave the way for a more sustainable future for the construction industry.
How Sustainable is Steel in Construction?
References and Further Reading
Kamaruddin, M. A., Abdullah, M. M. A., Zawawi, M. H., Zainol, M. R. R. A. (2017). Potential use of plastic waste as construction materials: recent progress and future prospects. In IOP Conference Series: Materials Science and Engineering, 267 (1), 012011. https://iopscience.iop.org/article/10.1088/1757-899X/267/1/012011/meta
Oberti, I., & Paciello, A. (2022). Bioplastic as a Substitute for Plastic in Construction Industry. Encyclopedia, 2(3), 1408-1420. https://doi.org/10.3390/encyclopedia2030095
Naimušin, A., & Januševičius, T. (2023). Development and Research of Recyclable Composite Metamaterial Structures Made of Plastic and Rubber Waste to Reduce Indoor Noise and Reverberation. Sustainability, 15(2), 1731. https://doi.org/10.3390/su15021731
Skoratko A, Katzer J. (2021). Harnessing 3D Printing of Plastics in Construction—Opportunities and Limitations. Materials; 14(16), 4547. https://doi.org/10.3390/ma1416454
Disclaimer: The views expressed here are those of the author expressed in their private capacity and do not necessarily represent the views of AZoM.com Limited T/A AZoNetwork the owner and operator of this website. This disclaimer forms part of the Terms and conditions of use of this website.