Corrosion analysis is crucial for predicting a material's resistance, comparing various materials, and assessing the behavior of a material in a corrosive setting. X-ray fluorescence (XRF) is a non-destructive, efficient, adaptable, sensitive, and multi-elemental analytical approach that is employed to determine the elemental composition of materials. This article focuses on the application of XRF to corrosion analysis.
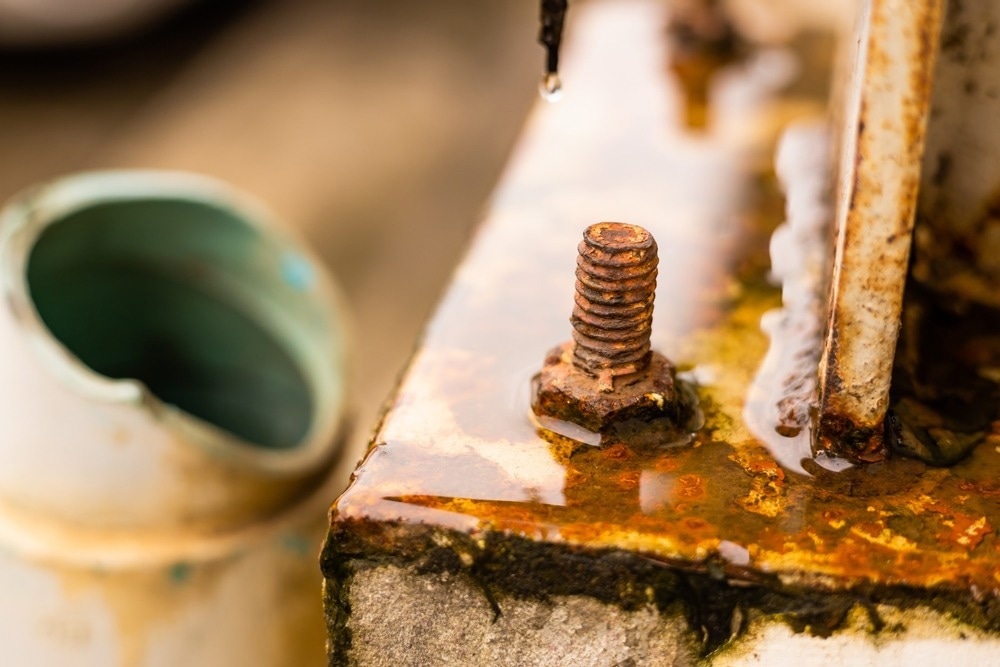
Image Credit: Quality Stock Arts/Shutterstock.com
Corrosion Analysis in Metal Structures
Metals typically exist in a compound state and can be separated into individual elements through the application of energy. This process results in a decrease in free energy and an increase in entropy. Consequently, atoms in a high-energy (metastable) excited state seek to return to a low-energy stable state. The most efficient way to achieve this is through oxidation, which occurs through the exchange of electrons between the metal and its surroundings.
Although various types of corrosion can occur, the main types include general corrosion, localized corrosion, and environmentally assisted cracking (EAC). The type of corrosion analysis and the consequent results depend on the type of corrosion.
The material degradation and loss of strength in metallic structures as a result of corrosion can have severe financial and safety implications. Among all the types of building structure destruction, the corrosion of metallic structures used in construction is considered the most detrimental. The chemical and electrochemical reactions associated with corrosion degrade the surface of the material and alter product quality.
Metals, particularly those used in load-bearing and roofing structures, are popular because of their technical advantages, such as precise manufacturing and simple assembly using high-strength bolts, making them a more attractive option than reinforced concrete structures. However, it is crucial to evaluate the properties and susceptibility of metals to corrosion before their use in construction.
Types of Corrosion and Their Analysis
General corrosion
This refers to the uniform loss of material from all the environment-exposed surfaces of a component. This type of corrosion can cause thinning of components, such as load-bearing or pressure-containing components, preventing them from performing their intended functions.
To assess general corrosion, a small representative sample of the material is prepared and exposed to the test environment for a specific time, depending on the design life of the component in question. After removal from the environment, the samples are weighed and measured again to determine the corrosion rate.
Environmentally Assisted Cracking (EAC)
This is the most severe form of corrosion that can lead to catastrophic failure of system components and is often undetectable by non-destructive evaluation methods. This phenomenon occurs when a susceptible material is subjected to stress.
To assess a material's susceptibility to EAC, it must be subjected to stress during testing, typically using tensile or C-ring specimens that are stressed between 80 and 100% of their yield stress. Upon removal of the samples from the environment, cracks and pits may be visible in the narrow section of the sample, called the gauge length.
If heavy corrosion is present, it may be necessary to shorten the duration of the cracking test or perform a general corrosion test instead, as the material may corrode before cracking becomes an issue.
Localized Corrosion
Pitting and crevice corrosion are two common forms of localized corrosion. Pitting is a localized corrosion that can deeply and rapidly penetrate a material's bulk and can be detected by visual evaluation.
Crevice corrosion occurs when fluid becomes trapped and cannot easily flow, causing the corrosion of components such as washers, nuts, and bolts. Artificial crevices are created to test for susceptibility, and the severity of corrosion is measured by evaluating the size and penetration depth of the crevices or pits.
XRF and its Application in Corrosion Analysis
XRF is a nondestructive, rapid, and versatile analytical method for determining the chemical composition of various samples, including solids, liquids, and powders. It does not require any sample preparation, making it suitable for both field and laboratory applications.
XRF is widely employed in various industries, such as archaeology, conservation, and metallurgy, to analyze and identify corrosion products, film compositions, and elemental concentrations. This technique is cost-effective and fast, making it an attractive option for researchers and professionals in different fields.
Archaeologists, museum curators, and conservators widely use XRF to gather crucial information about the artifacts under investigation. This technique can primarily be employed to identify corrosion products, which are essential for the conservation and management of priceless historical artifacts and archaeological collections. Corrosion-indicative elements that can be analyzed using XRF include nickel (Ni), copper (Cu), zinc (Zn), manganese (Mn), and titanium (Ti).
The advent of three-dimensional (3D) Micro-XRF has helped in quantitative corrosion analysis. Unlike conventional XRF, which measures the mass deposition, the 3D Micro-XRF provides information on local elemental densities as the samples’ properties.
Recent Studies
An article published in Corrosion Science utilized synchrotron XRF imaging and electron microscopy to investigate the mechanism of chloride-induced stress corrosion cracking (CISCC) in austenitic stainless steel welds 304 L-ER308L and 316 L-ER316L.
The study was conducted by exposing the specimens to a temperature of 60 °C and 30% relative humidity for three months and analyzing their microstructure and chemistry. The presence of delta (δ)-ferrite, which is composed of ferrite formers such as chromium, functioned as a sink for impurities, leading to the selective corrosion of δ-ferrite, resulting in pitting corrosion and CISCC propagation.
Another article published in Heritage examined a Late Iron Age earring found in the western part of the Iberian Peninsula. This earring exhibited a complex design featuring block- and strip-twisted wires and granulation.
The chemical composition and manufacturing methods of the earring were determined using multifocus optical microscopy, portable XRF, micro-XRF, and scanning electron microscopy integrated with energy dispersive spectroscopy (SEM-EDS).
The results revealed that the earring was crafted from an alloy of silver-rich wires and granules, which were encased by a 45 μm-thick gold-rich layer serving as an outer coating, presenting the appearance of being crafted from gold. This study provides an understanding of the methods employed by goldsmiths during the Iron Age for alloying.
Conclusion
In conclusion, XRF is a vital tool for analyzing corrosion in metallic structures because of its non-destructive and rapid nature in identifying elemental composition with precision, making it a highly effective and powerful method for assessing and comprehending corrosion mechanisms.
More from AZoBuild: Using Mass Spectrometry to Test Proposed Site Samples
References and Further Reading
Al-Sherrawi, M. H., Lyashenko, V., Edaan, E. M., Sotnik, S. (2018). Corrosion of metal construction structures. http://openarchive.nure.ua/handle/document/11922
Serrano, S., Rodrigues, A., Silva, R. J., Figueiredo, E. (2023). Study of an Iron Age Gilded Silver Earring by XRF, SEM-EDS and Multifocus OM. Heritage, 6(5), 4187-4201. https://doi.org/10.3390/heritage6050220
Kim, S., Ahn, K., Kim, G., Song, S. W. (2023). Synchrotron X-ray fluorescence imaging study on chloride-induced stress corrosion cracking behavior of austenitic stainless steel welds via selective corrosion of δ-ferrite. Corrosion Science, 218, 111176. https://doi.org/10.1016/j.corsci.2023.111176
Disclaimer: The views expressed here are those of the author expressed in their private capacity and do not necessarily represent the views of AZoM.com Limited T/A AZoNetwork the owner and operator of this website. This disclaimer forms part of the Terms and conditions of use of this website.