Concrete is a composite material consisting of cement, fine aggregate, and coarse aggregates. Unfortunately, cement ingredients are costly and negatively impact the environment due to hazardous carbon dioxide emissions. As a result, scientists and researchers are looking for environment-friendly building materials.
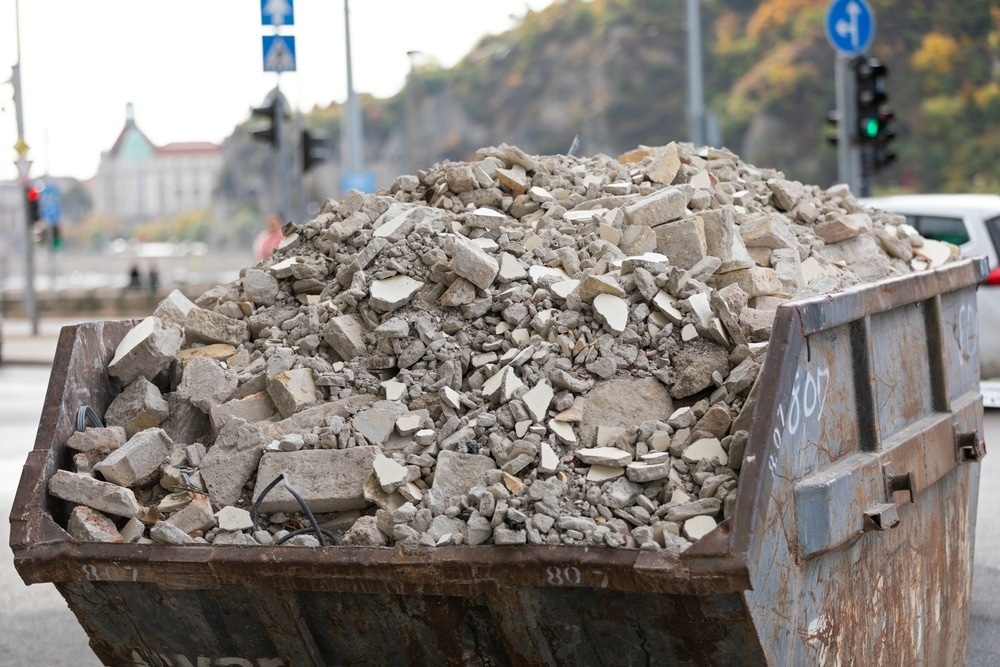
Image Credit: Ocskay Mark/Shutterstock.com
Urbanization, rapid industrialization, and population increase produce tons of trash globally. Unfortunately, most waste products cannot be recycled and are often managed by burning them or depositing them in landfills. Thus, alternative substitutes from waste materials can help resolve these challenges.
Waste materials are divided into different categories depending on the nature and source of the waste materials.
Glass Powder (GP)
Glass scraps are disposed of in landfills. Since glass cannot decompose, this technique is not sustainable from an environmental standpoint. Glass has recently been discovered to have cementitious qualities when ground to a specific fineness due to a pozzolanic reaction.
Experimental observations presented in a paper published in the European Journal of Environmental and Civil Engineering showed that adding 30 % GP is an ideal replacement that can provide comparable strength and even better workability.
Test samples were produced with 15%, 30%, and 50% of the GP in total weight of the concrete mix. No matter the curing condition or age mixes, the samples containing 15% and 30% GP demonstrated greater than 75% strength activity index values.
Organic Waste
Organic wastes are one of the most abundantly produced wastes. This could include wood ash, bagasse ash (a byproduct of sugar mills), or urban waste.
Urban waste (UW) accumulation caused by urbanization has raised more questions about how to make cities more sustainable. The World Bank estimates that annually 2.01 billion tons of UWs are produced worldwide. As a result, city administrators are forced to develop efficient waste management plans for the sheer volume of waste items.
UW can partially or entirely replace raw materials like aggregate and chemical admixtures used in manufacturing concrete, which minimizes the environmental burden of concrete production and prevents a high level of greenhouse gas emissions.
In addition to urban waste, studies have been conducted to utilize fallen leaves in concrete production. Palm leaves were ground and added to the concrete mixture in percentages of 10, 20, and 30%. The sample containing 10% leaf particles observed the highest compressive and bending strength.
Industrial Waste
Several industrial wastes exist, but the following three are the most commonly used as supplementary cementitious materials (SCMs). Depending on the applications and properties required, these can be used individually or in combination.
Fly Ash (FA)
Coal-fired power plants are the largest electricity source in the world, generating 38% of total electricity. As a result, disposing of waste fly ash (FA) from these power plants is a major problem worldwide.
In a study published in the Journal of Materials Today: Proceedings in 2022, researchers produced concrete samples with 5, 10, and 20% fly ash and 35% sand, and the rest was cement and analyzed the effects of fly-ash percentage on the properties of concrete.
The results indicated that a 20% fly ash mix with a longer curing time appeared valuable from an environmental and economic perspective. In contrast, a 5% fly ash mix could provide an early setting of cement concrete mix after seven days with excellent crushing strength. This strength increased further by increasing the number of days for curing, with the highest strength being achieved in 28 days.
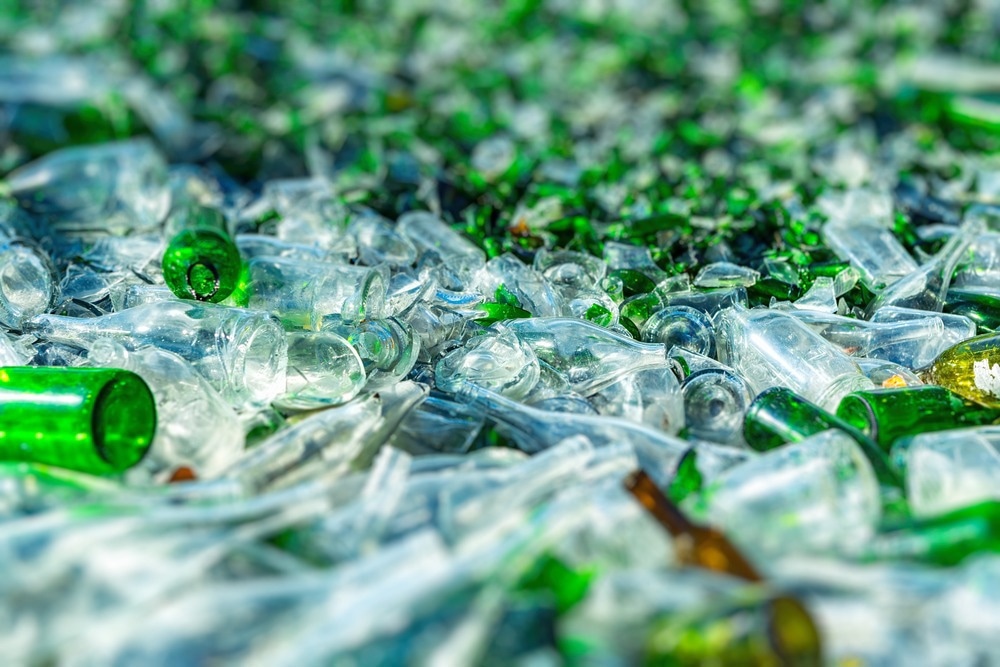
Image Credit: pixinoo/Shutterstock.com
Silica Fume (SF)
A byproduct of the smelting procedure used to create ferrosilicon alloys and elemental silicon is silica fume (SF). It is a highly amorphous type of silicon dioxide (SiO2) that contains tiny spherical SiO2 particles.
Reni Suriyanita et al. studied the effects of adding different percentages of SF into cellular lightweight concrete (CLC) and used SF weight percentages of 0, 0.5, 1, 5, 10, and 15%. The optimum compressive strength was 1.16 MPa for a 10% SF sample, which was 81.25% more than foam concrete. While adding more than 20% SF can decrease the strength of CLC, a balance is essential.
Blast Furnace And Other Slags
Iron and steel production in blast furnaces and other furnaces creates various slags. Generally, when quenched with water in its molten state, the blast furnace slag forms glassy granulated particles, which, after grinding, become ground granulated blast furnace slag (GGBS). Similarly, smelting of copper also produces copper slag.
A study shows that substituting slag for limestone particles in concrete can significantly boost the material's compressive strength. Compared to equivalent concretes created simply with natural aggregates that do not surpass a compressive strength of 40 MPa, concrete specimens constructed with slags showed a strength of up to 83 MPa.
Conclusion
In order to produce high-strength and high-performance concrete, supplementary cementitious materials (SCMs) such as fly ash, ground granulated blast-furnace slag, silica fume, and metakaolin are increasingly being used as binders for concrete. This article provides a brief overview of the use and effects of these materials in the construction industry.
The selection of waste material and its percentage are of utmost importance, as each combination will exhibit unique properties. For example, in some cases, adding plastic fiber into concrete can reduce flowability and may decrease the compressive and tensile strength of the mixture.
One of the most crucial elements is that the building's carbon footprint is decreased through the reuse of waste materials and the avoidance of traditional aggregates, which will greatly impact how the construction industry develops in the future.
More from AZoM: What To Know About Bioengineered Construction Materials
References and Further Reading
Kalakada, Zameer, J.H. Doh and S. Chowdhury (2022). Glass powder as replacement of cement for concrete – an investigative study. European Journal of Environmental and Civil Engineering, 26:3, 1046-1063, https://doi.org/10.1080/19648189.2019.1695149
O. Y. Bayraktar , M. Yılmazoğlu , İ. Mütevelli , M. Çetin , G. Sağlam Çitoğlu , C. P. Dadula and D. P. Dadula, (2022). Usability of organic wastes in concrete production; Palm leaf sample. Kastamonu University Journal of Engineering and Sciences, 8, no. 1, pp. 69-77, http://doi.org/10.55385/kastamonujes.1104531
Behl, Vishal, V. Singh, V. Dahiya, A. Kumar, (2022). Characterization of physico-chemical and functional properties of fly ash concrete mix. Journal of Materials Today: Proceedings, 50, No. 5, 941-945, https://doi.org/10.1016/j.matpr.2021.06.353.
Suryanita, Reni, H. Maizir, R. Zulapriansyah, Y. Subagiono, Mohd. F. Arshad, (2022). The effect of silica fume admixture on the compressive strength of the cellular lightweight concrete.Journal of Results in Engineering,14, https://doi.org/10.1016/j.rineng.2022.100445.
Petrounias, Petros, A. Rogkala, P. P. Giannakopoulou, A.Christogerou, P. Lampropoulou, S. Liogris, P. Koutsovitis, and N. Koukouzas, (2022). Utilization of Industrial Ferronickel Slags as Recycled Concrete Aggregates.Journal of Applied Sciences 12, no. 4: 2231. https://doi.org/10.3390/app12042231.
Ahmad, Jawad, A. Majdi, A. B. Elhag, A. F. Deifalla, M. Soomro, H. F. Isleem, and S. Qaidi, (2022). A Step towards Sustainable Concrete with Substitution of Plastic Waste in Concrete: Overview on Mechanical, Durability and Microstructure Analysis. Journal of Crystals 12, no. 7: 944. https://doi.org/10.3390/cryst12070944.
Disclaimer: The views expressed here are those of the author expressed in their private capacity and do not necessarily represent the views of AZoM.com Limited T/A AZoNetwork the owner and operator of this website. This disclaimer forms part of the Terms and conditions of use of this website.