Rubberized concrete is made by mixing crumbs of high-strength rubber – often from waste tires – into the aggregate mix with water and cement. While the compound is not particularly new, a new generation of researchers is now focused on experimentally verifying rubberized concrete’s properties to enable the more widespread use of a potentially greener construction material.
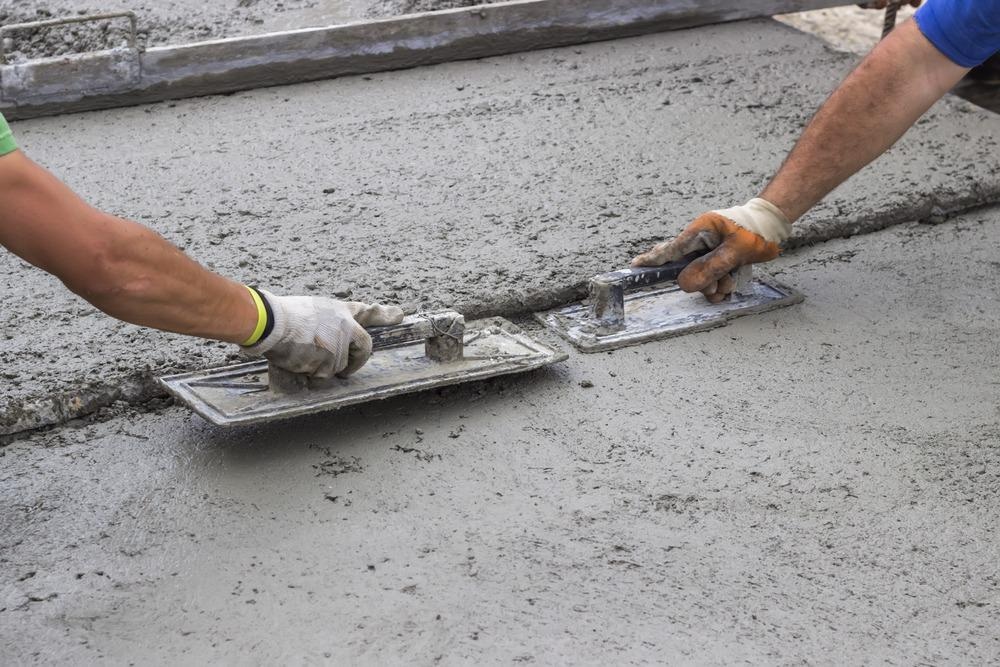
Image Credit: serato/Shutterstock.com
End-of-Life Tires are a Worldwide Waste Problem
Every year, billions of tires reach their end of life and have to be discarded. Tires are made from rugged, hard-wearing rubber, so disposing of them presents significant environmental challenges. They are not easily recycled, they break up into crumbs that are difficult to repurpose, and they will not biodegrade.
The United States alone disposes of 246 million to 300 million used tires each year. Globally, the problem is quantified at between 1 billion and 1.8 billion used tires every year, according to various studies. This makes up between 2% and 3% of all the waste collected on Earth.
A study in Australia found that only 5% of disposed-of tires were recycled in one year. Almost half were completely unaccounted for or dumped illegally, 16% were disposed of in official landfill sites, and 32% were sent overseas (likely to cheaper landfill sites).
The tire waste problem will grow as the world’s population grows – especially as a growing middle-class population in poorer countries creates a larger market for personal transportation.
Rubberized Concrete
Due to the growing problem with waste tires worldwide, researchers are now focused on making rubberized concrete a widely used, greener construction material.
Rubberized concrete contains chipped waste tires as an aggregate at varying rates of fill, depending on the desired properties. As well as end-of-life tires, rubberized concrete can use waste hoses, cables, and any other synthetic rubber products.
How is Rubberized Concrete Made?
There are two processes that manufacturers can use to make rubberized concrete: wet and dry.
In the wet process, finely ground tires are combined with an asphalt binder using high temperatures. The asphalt binder will generally contain about 10% recycled rubber by weight. The compound binding material is then mixed with cement and aggregate to make a rubberized asphalt.
The dry process is cheaper than the wet process and involves mixing aggregate with crumb rubber in a hot mix. Bitumen is then added to the mixture.
Properties of Rubberized Concrete
Early research on rubberized concrete in the 1990s found that the addition of rubber to a concrete mixture decreased the material’s flexural and compressive strengths. It also exhibited signs of cracking more often than conventional concrete due to low bonding performance between rubber materials and other contents in the concrete mix.
On the other hand, researchers found that, compared with conventional concrete, rubberized concrete displayed high toughness, a good capacity for plastic energy, strong durability, low porosity, abrasion resistance, and low density.
Recent advances in rubberized concrete studies have found that with the optimal manufacturing process involved, the material can actually display better crack resistance than conventional concrete as well. This is because the rubber in the material can delay cracking due to its flexural behavior.
Rubberized concrete is also better at resisting tensile stress than conventional concrete. This makes it relatively flexible, which means it can withstand severe impacts like a shot bullet more effectively.
A key feature of rubberized concrete is also its potential for environmental benefit. There are few solutions available for the significant and growing tire waste problem, and rubberized concrete may be a viable way to close this large waste loop.
What are the Applications of Rubberized Concrete?
These properties make rubberized concrete very well suited for a number of concrete applications. Footings and slabs – base layers of concrete for buildings and infrastructure projects – make up 40% of all concrete consumption in Australia, for example. They make good applications for ruggedized concrete, as they have lower requirements for mechanical strength.
The flexibility of rubberized concrete also makes it a good candidate for impact absorption applications. In highway construction, it can be used as a shock absorber and as an earthquake wave dampener in buildings.
Rubberized concrete also makes a good sound absorber. Rubber sound absorptive walls represent an efficient way for buildings to soundproof rooms or create acoustically performative spaces.
The Future for Rubberized Concrete
The focus of much recent research on rubberized concrete has been to establish an experimentally verified database of its engineering properties. This can now be used by forward-thinking engineers and designers to create buildings, infrastructure projects, and other large structures using rubberized concrete.
In turn, this can create market demand for the material, ultimately resulting in fewer waste tires – and other ruggedized rubber items – being sent to landfill sites.
Researchers still have work to do to optimize the material and its manufacturing processes. Pretreating rubber particles with chemical or mechanical treatments could improve cohesion with concrete particles and result in a stronger final material, for example.
More from AZoM: How is Foam Concrete Used in Construction?
References and Further Reading
Al-Balhawi, A., et al. (2022). Numerical Simulations on the Flexural Responses of Rubberised Concrete. Buildings. https://www.mdpi.com/2075-5309/12/5/590
Mills, J., et al. (2018). Crumbed Rubber Concrete: A Promising Material for Sustainable Construction. Scientia. doi.org/10.26320/SCIENTIA245.
Pilkington, B. (2021). Tackling the Global Tire Waste Problem with Pretred. [Online] AZO CleanTech. Available at: https://www.azocleantech.com/article.aspx?ArticleID=1227
Topçu, İ.B., and A. Unverdi (2018). Scrap tires/crumb rubber. Waste and Supplementary Cementitious Materials in Concrete. https://www.sciencedirect.com/science/article/pii/B978008102156900002X?via%3Dihub
Xue, J. and M. Shinozuka (2013). Rubberized concrete: A green structural material with enhanced energy-dissipation capability. Construction and Building Materials. https://www.sciencedirect.com/science/article/pii/S0950061813000688?via%3Dihub
Disclaimer: The views expressed here are those of the author expressed in their private capacity and do not necessarily represent the views of AZoM.com Limited T/A AZoNetwork the owner and operator of this website. This disclaimer forms part of the Terms and conditions of use of this website.