Due to the increasing number of automobiles, millions of tires are produced each year. Scrap tires are made up of nylon fiber and scrap tire rubber. One of the most effective ways to dispose of used tire rubber and nylon fiber is to recycle them in asphalt pavement, which is discussed in a study in the journal Buildings.
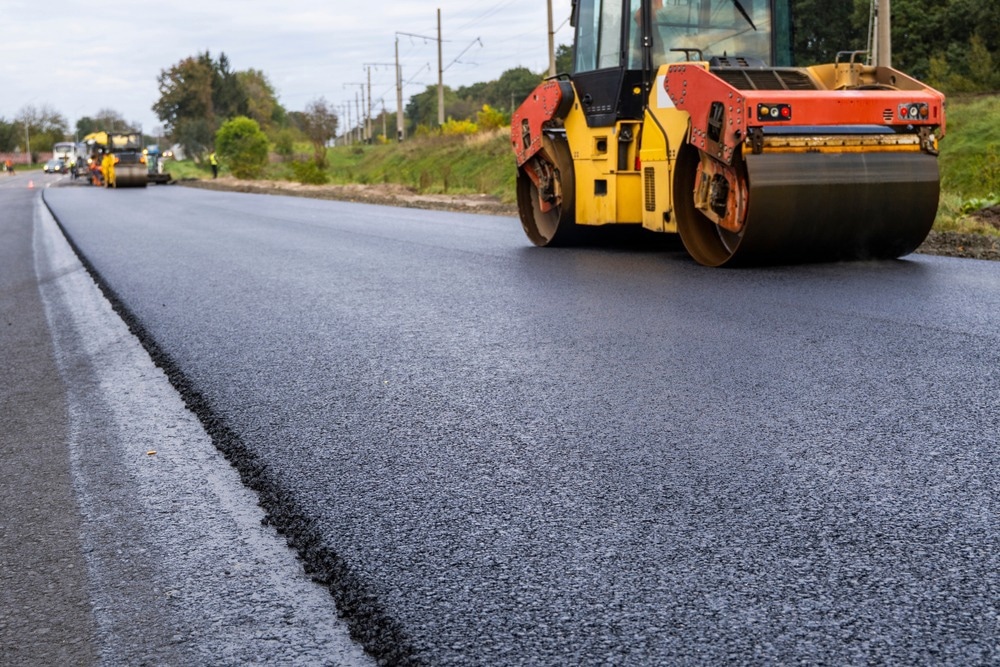
Study: Asphalt Mixture with Scrap Tire Rubber and Nylon Fiber from Waste Tires: Laboratory Performance and Preliminary M-E Design Analysis. Image Credit: Volodymyr_Shtun/Shutterstock.com
Scientists have discovered that adding nylon fiber to a stone matrix asphalt mixture increased high-temperature deformation resistance and low-temperature cracking resistance. Meanwhile, as an alternative, asphalt mixing temperature reduction technology is gaining popularity.
Researchers investigated the characteristics of scrap rubber modified warm mix asphalt pavement and discovered that the warm mix asphalt helped to minimize asphalt and fuel consumption as well as harmful pollutants.
Furthermore, when compared to scrap rubber hot mix asphalt mixture, the warm mix asphalt mixture has similar resistance to high-temperature deformation and low-temperature cracking, as well as improved fatigue characteristics.
Warm mix additives in asphalt mixtures can assist lower temperature by 30 °C during mixing and compaction, and warm mix technology can help reduce CO2 emissions. Many scientists have explored scrap rubber combined with asphalt mixture via the wet method, dry mix, or terminal blend.
The primary goal of this study was to look at the qualities of waste tire rubber and a warm asphalt mixture that had been amended with nylon fibers. Hamburg wheel track testing (HWTT) was used to calculate the high-temperature characteristics. The disk shape compact tension (DCT) and indirect tensile strength (IDT) tests were used to assess low-temperature cracking performance.
At various temperatures and frequencies, the dynamic modulus test was used to analyze the stress-strain relationship. Using a dynamic shear rheometer, the removed asphalt binder was analyzed (DSR). Pavement M.E. study predicted pavement distress. The current work demonstrates the impact of scrap tire rubber and nylon fiber modified warm mix asphalt mixture based on laboratory performance and ME design analysis.
Methodology
The flexible pavement’s aggregate gradation is shown in detail in Figure 1.
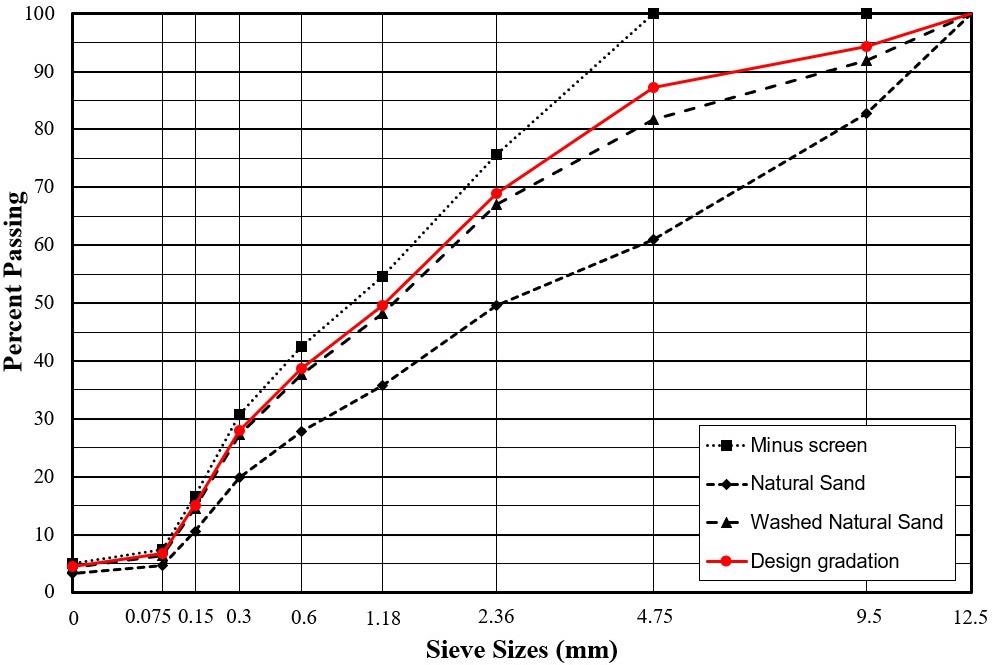
Figure 1. Aggregate gradation of the selected asphalt mixtures. Image Credit: Jin, et al., 2022
Figure 2 depicts the scrap rubber and nylon fiber utilized in the project.
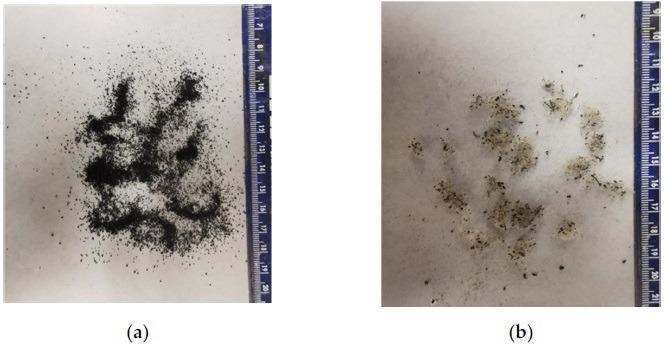
Figure 2. Scrap tire rubber and nylon fiber that were used in this study: (a) scrap tire rubber, (b) nylon fiber. Image Credit: Jin, et al., 2022
The waste tire rubber and nylon fiber modified heated asphalt mixture was crushed to a 7% air void using the Superpave gyratory compactor. Figure 3 depicts the preparation procedure in detail.
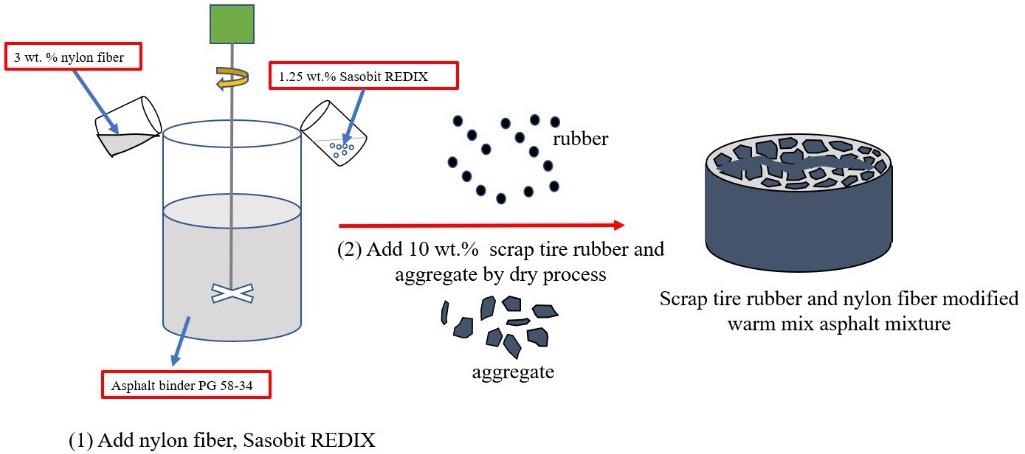
Figure 3. Preparation of scrap tire rubber and nylon fiber modified WMA. Image Credit: Jin, et al., 2022
Figure 4 depicts the technical flowchart, which is followed by a description of the specifications.
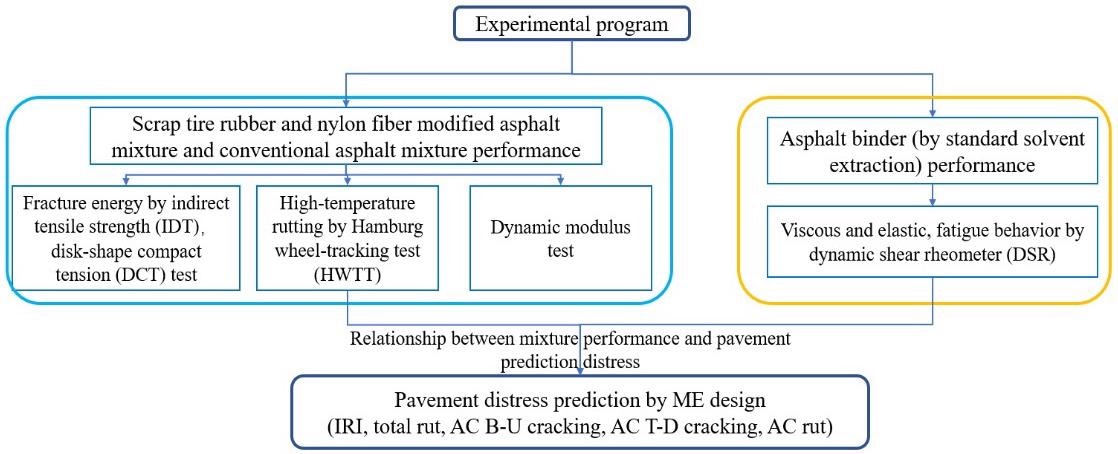
Figure 4. The technical flowchart of this study. Image Credit: Jin, et al., 2022
The pavement design information used for this road is detailed in Table 1.
Table 1. Pavement structure and thickness used in this study. Source: Jin, et al., 2022
Layer Types and Thickness |
Pavement Structure |
Surface layer (3.8 cm) |
Conventional or rubber and nylon fiber modified warm mix asphalt (WMA) |
Leveling course (5 cm) |
Dense mix asphalt mixture |
Asphalt base course (17.8 cm) |
Dense mix asphalt mixture |
Aggregate base (15.2 cm) |
Sandwich granular |
Aggregate base (25.4 cm) |
Crushed stone |
Aggregate subbase (15.2 cm) |
Crushed gravel |
subgrade |
Semi-infinite |
Note: The surface layer Pavement ME Design inputs are based on the laboratory test results. All the left layer Pavement ME Design inputs are based on the recommended reference value from MDOT.
Results and Discussion
Figure 5 shows the complex shear modulus (|G*|) and phase angle master curves of the basic asphalt binder and extract asphalt binder. The complex shear modulus (|G*|) and phase angle of the PAV-aged asphalt binder are shown in Figure 5(a). Figure 5(b) shows the complex shear modulus (|G*|) and phase angle findings of the RTFO-aged asphalt binder.
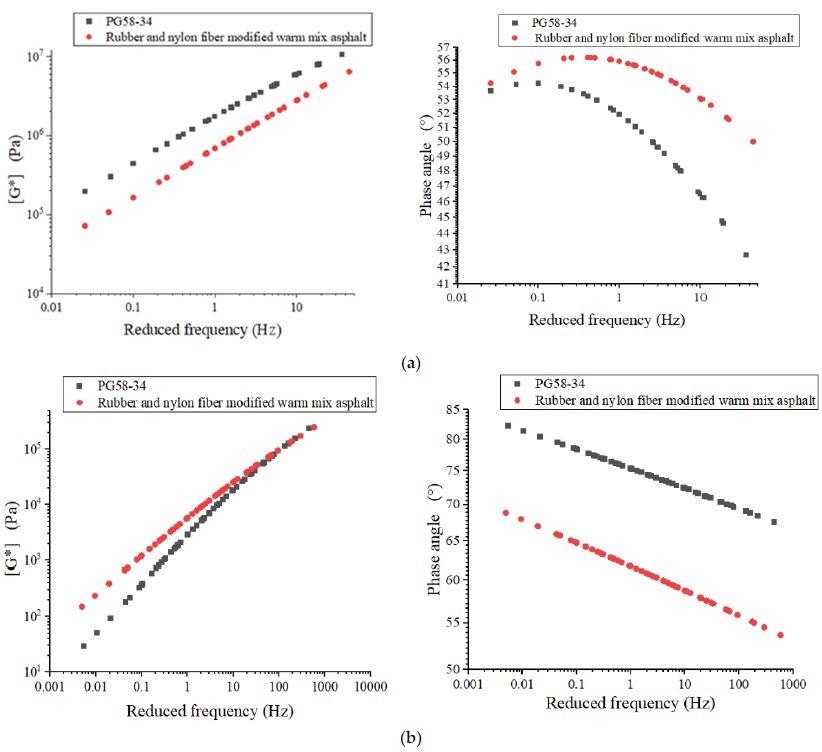
Figure 5. The master curve of different types of asphalt binder: (a) The complex shear modulus (left)and phase angle (right) master curve at 19° C (PAV aged), (b) The complex shear modulus (left)and phase angle (right) master curve at 58° C (RTFO aged). Image Credit: Jin, et al., 2022
Figure 6 shows the findings of the disc-shaped compact tension test at low temperatures. Figure 6(a) shows the DCT test load versus displacement curve. Figure 6(b) shows the fracture energy of rubber and nylon fiber modified WMA and traditional HMA.
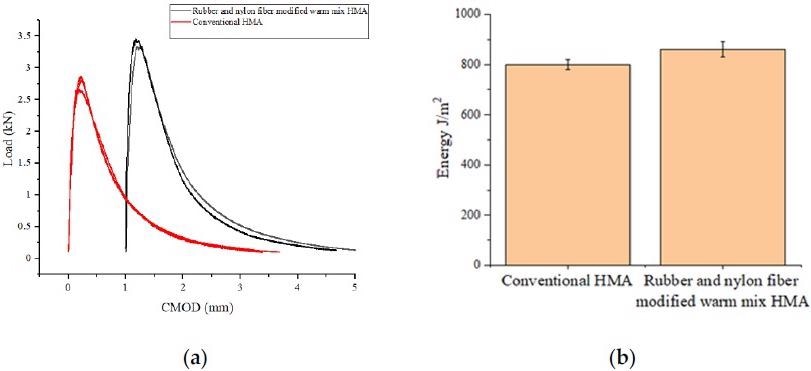
Figure 6. The DCT test results and fracture energy of various sorts of HMA: (a) DCT test results, (b) fracture energy results. Image Credit: Jin, et al., 2022
Figure 7 depicts the HWDT findings of rubber and nylon fiber modified WMA and regular HMA.
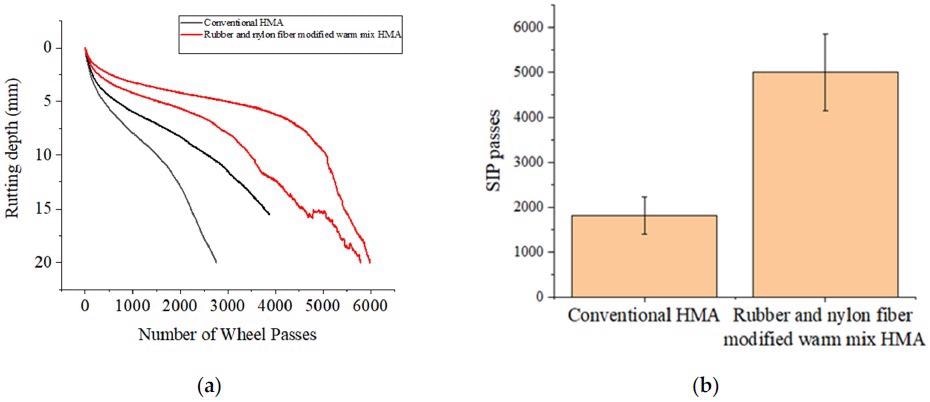
Figure 7. The HWDT test results of different types of asphalt mixture: (a) rutting depth vs. the number of wheel passes, (b) SIP passes results of various types of asphalt mixture. Image Credit: Jin, et al., 2022
Figure 8 shows the dynamic modulus master curves for nylon fiber modified WMA and standard asphalt mixture.
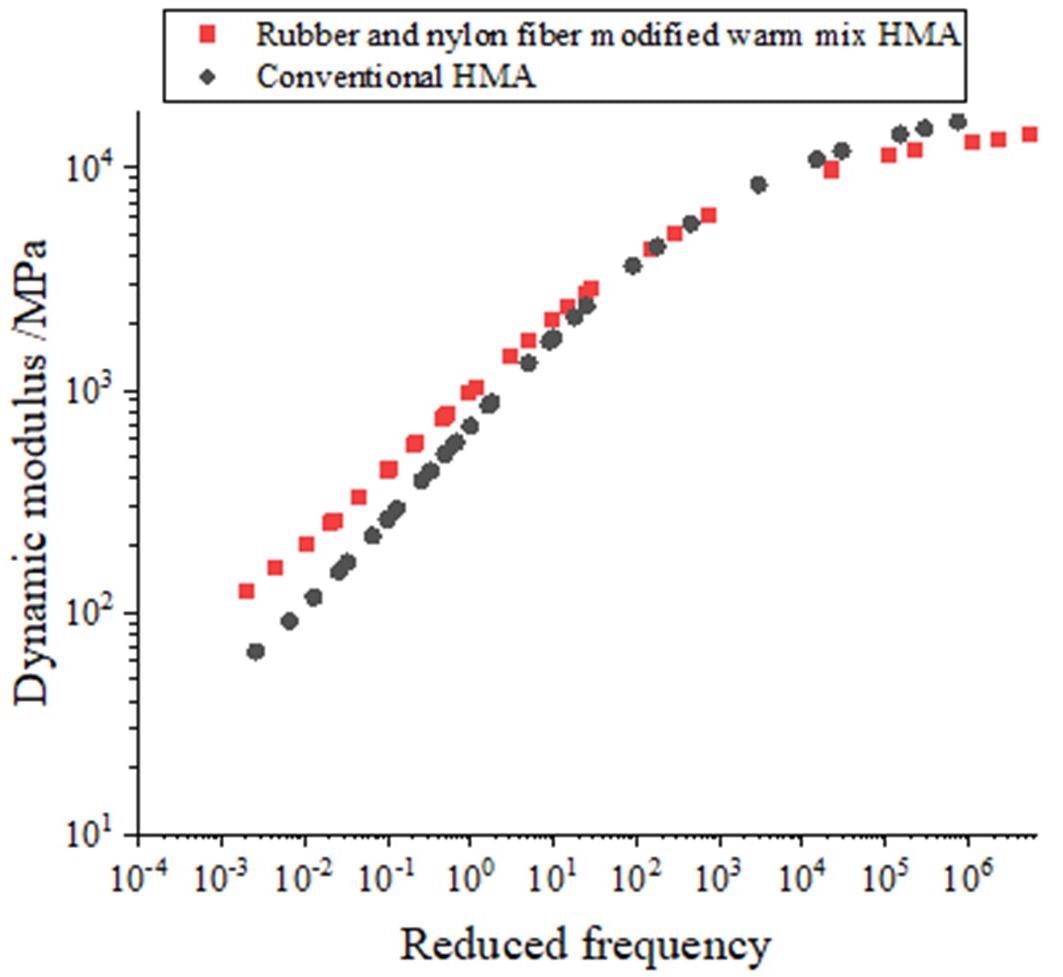
Figure 8. Dynamic modulus Master curve at 21 °C for different types of asphalt mixture. Image Credit: Jin, et al., 2022
Figure 9 shows the indirect tensile strength values of rubber and nylon fiber adapted WMA and traditional HMA.
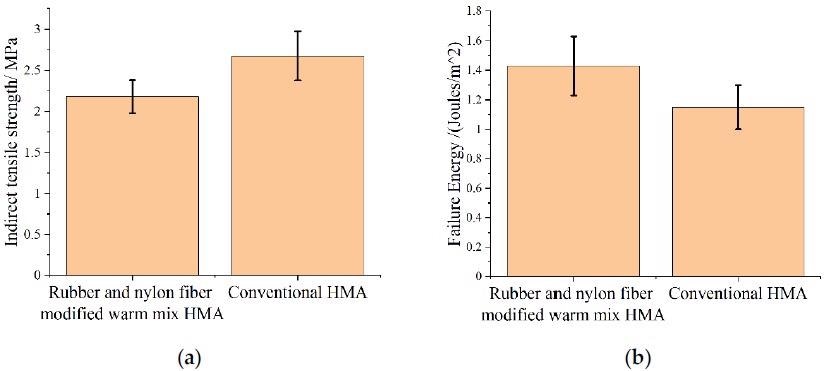
Figure 9. IDT strength and failure energy for various types of HMA: (a) IDT strength for different types of asphalt mixture, (b) failure energy for different types of asphalt mixture. Image Credit: Jin, et al., 2022
Figure 10 depicts the pavement distress prediction results of rubber and nylon fiber adapted WMA and traditional HMA.
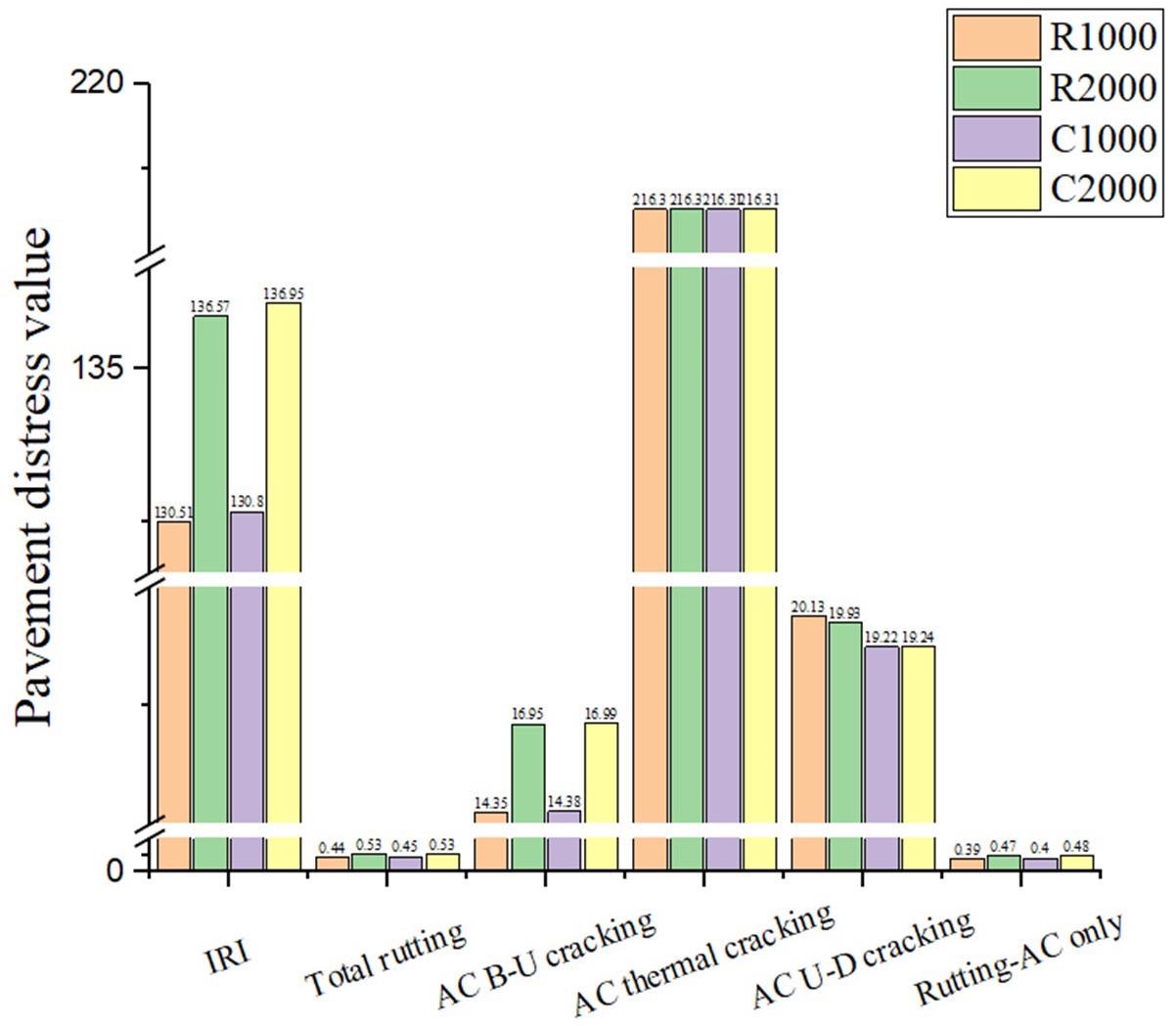
Figure 10. Pavement distress prediction results for different types of asphalt mixture. Note: R1000means rubber and nylon fiber modified WMA at 1000 AADTT traffic levels. R2000 means rubber and nylon fiber modified WMA at 2000 AADTT traffic level. C1000 means conventional HMA at1000 AADTT traffic level. C2000 means conventional HMA at 2000 AADTT traffic, IRI smoothness (in/mile or 0.016 m/km), total rut (in or 0.0254 m), AC B-U (bottom-up) cracking (% lane area), and AC rut (in or 0.0254 m). Image Credit: Jin, et al., 2022
Tables 2 and 3 provide the ME input data for rubber and nylon fiber modified WMA and regular HMA.
Table 2. Pavement ME Design inputs for rubber and nylon fiber modified WMA. Source: Jin, et al., 2022
E*(MPa) Average Value Rubber and Nylon Fiber Modified WMA |
|
F (Hz) |
0.1 |
0.5 |
1 |
5 |
10 |
25 |
T (°C) |
-10 |
|
6463.2 |
8848.3 |
10,010.1 |
12,667.3 |
14,253.0 |
15,521.3 |
10 |
|
2180.8 |
3261.2 |
3935.8 |
5773.4 |
6679.5 |
7673.6 |
21 |
|
511.5 |
718.1 |
947.1 |
1620.4 |
2061.0 |
2645.0 |
37 |
|
210.9 |
261.8 |
321.9 |
492.2 |
610.3 |
862.9 |
54 |
|
120.0 |
181.0 |
309.0 |
498.1 |
606.6 |
773.3 |
G* (MPa) Average Value |
Creep Compliance |
Temperature (℃) |
|
Binder G* (Pa) |
Phase angle (℃) |
Time (sec) |
Temperature (℃) |
16 |
|
1,430,000 |
54.38 |
−20 |
−10 |
0 |
34 |
|
97,216 |
58.89 |
1 |
5.32 x 10−7 |
1.04 x 10−6 |
2.25 x 10−6 |
46 |
|
25,659 |
58.27 |
2 |
5.87 x 10−7 |
1.21 x 10−6 |
2.69 x 10−6 |
64 |
|
4435 |
60.38 |
5 |
6.86 x 10−7 |
1.46 x 10−6 |
3.50 x 10−6 |
76 |
|
1629 |
64.83 |
10 |
7.75 x 10−7 |
1.74 x 10−6 |
4.24 x 10−6 |
(−10 ℃) IDT strength: 2.676 MPa |
20 |
8.75 x 10−7 |
2.07 x 10−6 |
5.18 x 10−6 |
50 |
1.06 x 10−6 |
2.59 x 10−6 |
6.94 x 10−6 |
100 |
1.22 x 10−6 |
3.15 x 10−6 |
8.56 x 10−6 |
Table 3. Pavement ME Design inputs for conventional HMA. Source: Jin, et al., 2022
E*(MPa) Average Value Conventional HMA |
|
F (Hz) |
0.1 |
0.5 |
1 |
5 |
10 |
25 |
T (°C) |
−10 |
|
6821.2 |
9806.8 |
11,183.8 |
14,234.0 |
15,584.8 |
16,782.7 |
10 |
|
2548.0 |
4570.4 |
5806.5 |
8961.4 |
10,779.7 |
12,600.4 |
21 |
|
296.5 |
512.7 |
600.3 |
1081.1 |
1476.7 |
2032.4 |
37 |
|
142.6 |
182.0 |
219.4 |
444.7 |
532.5 |
755.6 |
54 |
|
60.0 |
100.0 |
152.0 |
352.0 |
498.0 |
582.0 |
G* (MPa) Average Value |
Creep Compliance |
Temperature (℃) |
|
Binder G* (Pa) |
Phase angle (°) |
Time (sec) |
Temperature (℃) |
16 |
|
3,146,800 |
48.63 |
−20 |
−10 |
0 |
34 |
|
78,249.67 |
68.16 |
1 |
4.35 x 10−7 |
7.94 x 10−7 |
1.95 x 10−6 |
46 |
|
16,972.33 |
71.25 |
2 |
4.64 x 10−7 |
8.93 x 10−7 |
2.35 x 10−6 |
64 |
|
2042.63 |
75.98 |
5 |
5.05 x 10−7 |
1.05 x 10−6 |
3.02 x 10−6 |
76 |
|
594.66 |
79.63 |
10 |
5.43 x 10−7 |
1.21 x 10−6 |
3.74 x 10−6 |
T(−10 ℃) IDT strength: 2.18 MPa |
20 |
5.92 x 10−7 |
1.41 x 10−6 |
4.69 x 10−6 |
50 |
6.65 x 10−7 |
1.74 x 10−6 |
6.32 x 10−6 |
100 |
7.34 x 10−7 |
2.09 x 10−6 |
8.12 x 10−6 |
Conclusion
The rubber and nylon fiber modified WMA had better stiffness than the regular asphalt mixture at high temperatures, which increased rutting resistance at high temperatures, according to the dynamic modulus test.
The rubber and nylon fiber modified warm mix asphalt has greater rutting resistance and fatigue performance than the base asphalt binder, according to the findings of the dynamic shear rheometer tests. The presence of rubber and nylon fiber particles in the asphalt increases the strength of the asphalt binder, improving deformation resistance and fatigue properties under load.
When compared to typical asphalt mixes, the rubber and nylon fiber-modified WMA exhibited a greater fracture resistance in IDT and DCT tests. The rubber and nylon fiber-modified WMA have greater rutting resistance and antistripping than the regular HMA.
In conclusion, using the rubber and nylon fiber modified WMA enhanced the functioning of asphalt pavement in terms of high-temperature rutting, low-temperature cracking resistance, and fatigue qualities.
Furthermore, the pavement ME analysis revealed a better forecast distress performance than the traditional HMA, implying that rubber and nylon fiber modified warm mix asphalt pavement might outperform conventional asphalt pavement on low traffic volume roads.
Journal Reference:
Jin, D., Ge, D., Zhou, X., You, Z (2022) Asphalt Mixture with Scrap Tire Rubber and Nylon Fiber from Waste Tires: Laboratory Performance and Preliminary M-E Design Analysis. Buildings, 12(2), p. 160. Available Online: https://www.mdpi.com/2075-5309/12/2/160
References and Further Reading
- Li, X., et al. (2021) High‐temperature creep and low‐temperature relaxation of recycled asphalt mixtures: Evaluation and balanced mix design. Construction and Building Materials, 310, p. 125222. doi.org/10.1016/j.conbuildmat.2021.125222.
- Chen, J., et al. (2021) New innovations in pavement materials and engineering: A review on pavement engineering research 2021. Journal of Traffic and Transportation Engineering (English Edition), 8, pp. 815–999. doi.org/10.1016/j.jtte.2021.10.001.
- Marconi, M., et al. (2018) Reuse of tires textile fibers in plastic compounds: is this scenario environmentally sustainable? Procedia CIRP, 69, pp. 944–949. doi.org/10.1016/j.procir.2017.11.074.
- Ge, D., et al. (2020) Laboratory Evaluation of the Residue of Rubber‐Modified Emulsified Asphalt. Sustainability, 12, p. 8383. doi.org/10.3390/su12208383.
- Ogunbiyi, A. W., et al. (2016) Smelting of Waste Nylon and Low‐density Plastics (ldps) in a Fluidized Bed System. Procedia Environmental Sciences, 35, pp. 491–497. doi.org/10.1016/j.proenv.2016.07.033.
- Wang, W., et al. (2017) Hydrolysis of waste monomer casting nylon catalyzed by solid acids. Polymer Degradation and Stability, 136, pp. 112–120. doi.org/10.1016/j.polymdegradstab.2016.12.017.
- Yin, J & Wu, W (2018) Utilization of waste nylon wire in stone matrix asphalt mixtures. Waste Management, 78, pp. 948–954. doi.org/10.1016/j.wasman.2018.06.055.
- Lee, S. J., et al. (2005) Fatigue Cracking Resistance of Fiber‐Reinforced Asphalt Concrete. Textile Research Journal, 75, pp. 123–128. doi.org/10.1177/004051750507500206.
- Taherkhani, H (2016) Investigating the effects of nanoclay and nylon fibers on the mechanical properties of asphalt concrete. Civil Engineering Infrastructures Journal, 49, pp. 235–249. doi.org/10.7508/ceij.2016.02.004.
- Yang, X., et al. (2017) Environmental and mechanical performance of crumb rubber modified warm mix asphalt using Evotherm. Journal of Cleaner Production, 159, pp. 346–358. doi.org/10.1016/j.jclepro.2017.04.168.
- Oliveira, J. R., et al. (2013) Use of a warm mix asphalt additive to reduce the production temperatures and to improve the performance of asphalt rubber mixtures. Journal of Cleaner Production, 41, pp. 15–22. doi.org/10.1016/j.jclepro.2012.09.047.
- Dinis‐Almeida, M & Afonso M L (2015) Warm mix recycled asphalt–a sustainable solution. Journal of Cleaner Production, 107, pp. 310–316. doi.org/10.1016/j.jclepro.2015.04.065.
- Airey, G. D., et al. (2003) Absorption of Bitumen into Crumb Rubber Using the Basket Drainage Method. International Journal of Pavement Engineering, 4, pp. 105–119. doi.org/10.1080/1029843032000158879.
- Rahman, M. M., et al. (2010) Moisture Susceptibility of High and Low Compaction Dry Process Crumb Rubber–Modified Asphalt Mixtures. Transportation Research Record: Journal of the Transportation Research Board, 2180, pp. 121–129. doi.org/10.3141/2180‐14.
- Chen, S., et al. (2020) Investigation of hot mixture asphalt with high ground tire rubber content. Journal of Cleaner Production, 277, p. 124037. doi.org/10.1016/j.jclepro.2020.124037.
- Xie, Z & Shen, J (2016) Fatigue Performance of Rubberized Stone Matrix Asphalt by a Simplified Viscoelastic Continuum Damage Model. Journal of Materials in Civil Engineering, 28, p. 04015162. doi.org/10.1061/(asce)mt.1943‐5533.0001463.
- Jin, D., et al. (2021) Cold In‐Place Recycling Asphalt Mixtures: Laboratory Performance and Preliminary M‐E Design Analysis. Materials, 14, p. 2036. doi.org/10.3390/ma14082036.
- Buch, N., et al. (2009) Characterization of truck traffic in Michigan for the new mechanistic empirical pavement design guide. Michigan. Department of Transportation Construction and Technology Division: Lansing, MI, USA.
- AASHTO T 342 (2011) Standard Method of Test for Determining Dynamic Modulus of Hot Mix Asphalt (HMA). American Association of State Highway Transportation Officials: Washington, DC, USA.
- ASTM D7313 ‐ 20 (2021) Standard Test Method for Determining Fracture Energy of Asphalt Mixtures Using the Disk‐Shaped Compact Tension Geometry. American Society for Testing and Materials International: West Conshohocken, PA, USA.
- AASHTO T 324 (2019) Standard Method of Test for Hamburg Wheel‐Track Testing of Compacted Asphalt Mixtures. American Association of State Highway Transportation Officials: Washington, DC, USA.
- AASHTO T 322 (2007) Standard Method of Test for Determining the Creep Compliance and Strength of Hot Mix Asphalt (HMA) Using the Indirect Tensile Test Device. American Association of State Highway Transportation Officials: Washington, DC, USA.
- Jin, D., et al. (2021) Waste cathode‐ray‐tube glass powder modified asphalt materials: Preparation and characterization. Journal of Cleaner Production, 314, p. 127949. doi.org/10.1016/j.jclepro.2021.127949.
- AASHTO T 315 (2020) Standard Method of Test for Determining the Rheological Properties of Asphalt Binder Using a Dynamic Shear Rheometer. American Association of State Highway Transportation Officials: Washington, DC, USA.
- AASHTO, T., (2009) Standard method of test for effect of heat and air on a moving film of asphalt binder (rolling thin‐film oven test). American Association of State Highway Transportation Officials: Washington, DC, USA.
- AASHTO, P., (2009) Standard practice for accelerated aging of asphalt binder using a pressurized aging vessel (PAV). American Association of State Highway Transportation Officials: Washington, DC, USA.
- MDOT, (2021) Michigan DOT User Guide for Mechanistic‐Empirical Pavement Design. Michigan Department of Transportation: Lansing, MI, USA.
- Park, S & Schapery, R (1999) Methods of interconversion between linear viscoelastic material functions. Part I—a numerical method based on Prony series. International Journal of Solids and Structures, 36, pp. 1653–1675. doi.org/10.1016/s0020‐7683(98)00055‐9.