Nov 8 2021
Buildings and structures in the Arctic and the Antarctic need to be protected against both cryogenic spills and fire exposure. This article analyzes three different structural fireproofing materials, as explored in the journal Buildings.
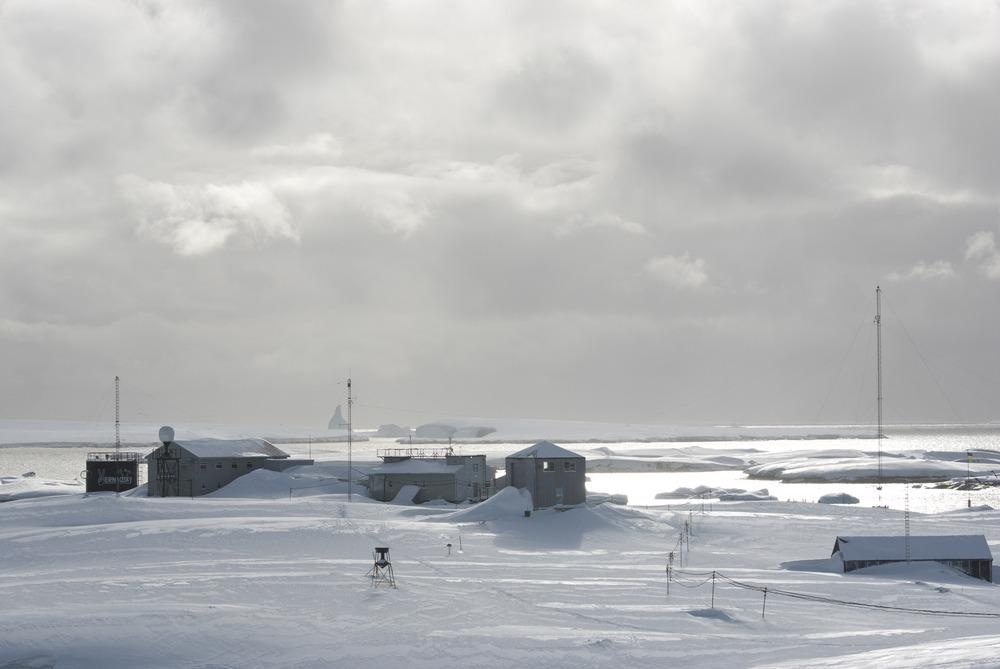
Research Station in Antarctica. Study: Structural Fire Protection of Steel Structures in Arctic Conditions. Image Credit: Tarpan/Shutterstock.com
The Arctic climate has minimum winter temperatures ranging from −54 °C to −71 °C, hence structures and buildings in the Arctic and Antarctic should be safeguarded with special materials—specifically fire retardants to increase their fire resistance limits, also after the filling of cryogenic liquid, such as liquid natural gas (LNG). Many technological disasters and fires also occur at Arctic stations, the bearing elements of which are steel structures.
Optimal solutions for the protection of steel structures in fires are with intumescent coatings. A major component of intumescent coating is the binder, which harbors numerous physical and chemical characteristics to enable a defect-free, quality, durable flame retardant coating. Another vital aspect of intumescent coating is its relative water solubility.
A simplified methodology can be used to analyze the thermo-mechanical behavior of an offshore structure under high temperatures, taking into account the presence of a passive fire protection (PFP) layer. The mechanical properties were analyzed using modified techniques and a database was developed to apply a series of nonlinear structural and thermal finite-element analyses of the PFP bulkhead marine system.
Figure 1 depicts the scheme of means and methods of fire protection of steel structures. It shows that the most preferred method of fire protection in the Arctic climate is the application of structural fire protection, the major advantage being “dry” installation and high fire resistance.
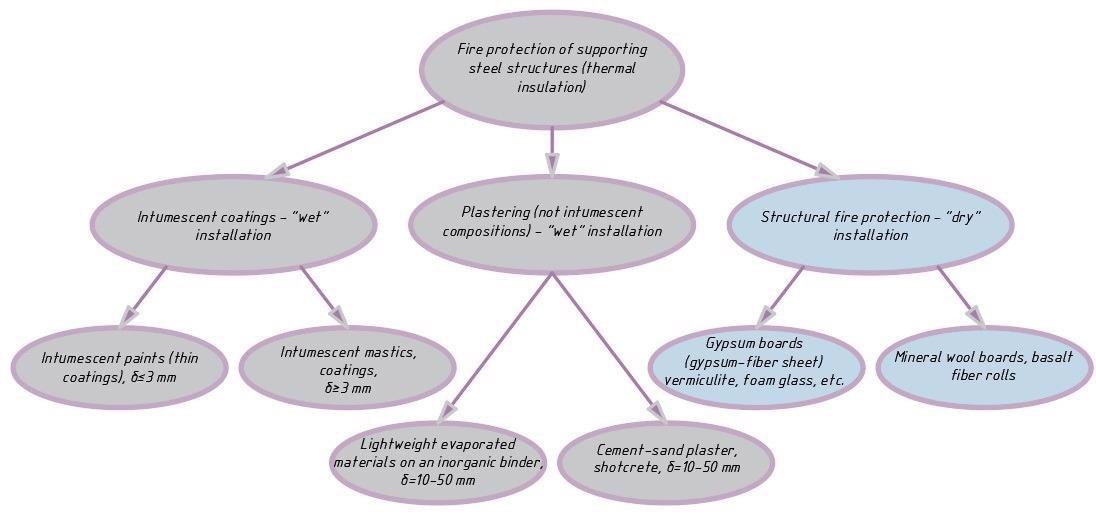
Figure 1. Means and methods of fire protection of steel structures. Image Credit: Gravit and Shabunina, 2021.
Super-thin basalt fibers (STBF) are a possible basis for thermal insulation materials and products. They are made exclusively from basalts without admixtures of other minerals. Owing to their numerous properties STBF based products are superior to their analogs. Table 1 compares the characteristics of various kinds of insulation wool.
Name of Parameters |
Slag Wool |
Glass Wool |
TBF |
STBF |
Limit temperature application, °C |
up to 250 |
from –60 to +450 |
from –190 to +700 |
from –190 to +1000 |
Sintering temperature, °C |
250–300 |
450–500 |
700–1000 |
1100–1500 |
Average fiber diameter, μm |
4 to 12 |
4 to 12 |
5 to 15 |
1 to 3 |
Length of fibers, mm |
16 |
15–50 |
20–50 |
50–70 |
Sorption humidification per 24 h. (max),% |
1.9 |
1.7 |
0.035 |
0.02 |
Using the binder |
yes |
yes |
yes |
no |
Presence of binder, % |
2.5 to 10 |
2.5 to 10 |
2.5 to 10 |
- |
Thermal conductivity coefficient, W/(m·K) |
0.46–0.48 |
0.038–0.046 |
0.03–0.046 |
0.035–0.046 |
Heat capacity, J/kg·K |
1000 |
1050 |
500–800 |
800–1000 |
Density, kg/m3 |
75–400 |
10–130 |
26–36 |
18–25 |
Sound absorption coefficient |
0.75 to 0.82 |
0.8 to 92 |
0.8 to 95 |
0.95 to 99 |
Vibration resistance |
no |
no |
no |
yes |
Table 1. Comparison of the characteristics of different types of insulation wool. Source: Gravit and Shabunina, 2021.
The article aims to analyze the structural protection based on STBF under operating conditions in the Arctic climate.
Fire retardant materials “PROMISOL-MIX PROPLEIT-50-K” (sample No. 1) and “BST-MAT” (sample No. 2) during fire test under a hydrocarbon temperature regime and fire retardant “3M Interam” (sample No. 3.1 and sample No. 3.2) during cryogenic exposure and a succeeding fire test under a hydrocarbon fire regime were considered.
Methodology
The experimental samples were examined under the conditions of developing a hydrocarbon temperature regime in the fire chamber of the furnace.
In samples No. 1 and No. 2, the temperature in the furnace’s firing chamber was analyzed by thermocouples, installed by caulking in the amount of three pieces in the average cross-section of the samples on the I-beam wall and on the inner surface of the flanges. For samples No. 3.1 and No. 3.2 six thermocouples were installed, three main and three duplicating, symmetrically to the main.
Experiment No. 1
Sample No. 1 is a steel column of I-shaped cross-section No. 20B1. The analyses were performed in the VNIIPO of the Ministry of Emergency Situations in Russia. Sample No. 1 was kept in the fire chamber of the furnace and subjected to four-sided heat exposure without static load until the limit state of the sample.
The fire chamber’s temperature was generated by the hydrocarbon fire regime and was measured with furnace thermocouples in five locations.
Experiment No. 2
Sample No. 2 was a steel column of an I-shaped cross-section, and the analyses were performed in the testing laboratory POZH-AUDIT.
Measurements of the actual thickness of the fire-retardant coating applied to the sample were carried out before the tests. Sample No. 2 was kept in the fire chamber of the furnace and had a four-sided heat exposure without static load.
Experiment No. 3
For experiment No. 3, two samples were examined. Sample No. 3.1 was a steel column of I-shaped cross-section No. 50B2 with flame-retardant coating, and Sample No. 3.2 was a steel column of I-shaped cross-section No. 50B2 and flame-retardant coating. The test was conducted at the test center Ognestoykost.
The tests of the samples were performed in two stages—the stage of cryogenic exposure and the stage of thermal exposure under hydrocarbon fire conditions and both the test stages were performed consecutively on the same day.
Liquid nitrogen is used as the liquid hydrocarbon analog as it has a lower boiling point than LNG or liquid oxygen and is not flammable. The analysis to find the time of attaining the critical state under cryogenic exposure was performed according to the regulations of ISO 20088-1.
To carry out the cryogenic test, a tank built of polystyrene foam (Figure 2) was attached to the surface of the fireproof mat strictly in the center of the I-beam flange using a flame-retardant sealant. Around 3.5 L of liquid nitrogen was poured into the tank, and to decrease the vaporization rate and the tank was covered with a sheet of polystyrene foam 50 mm thick from above.
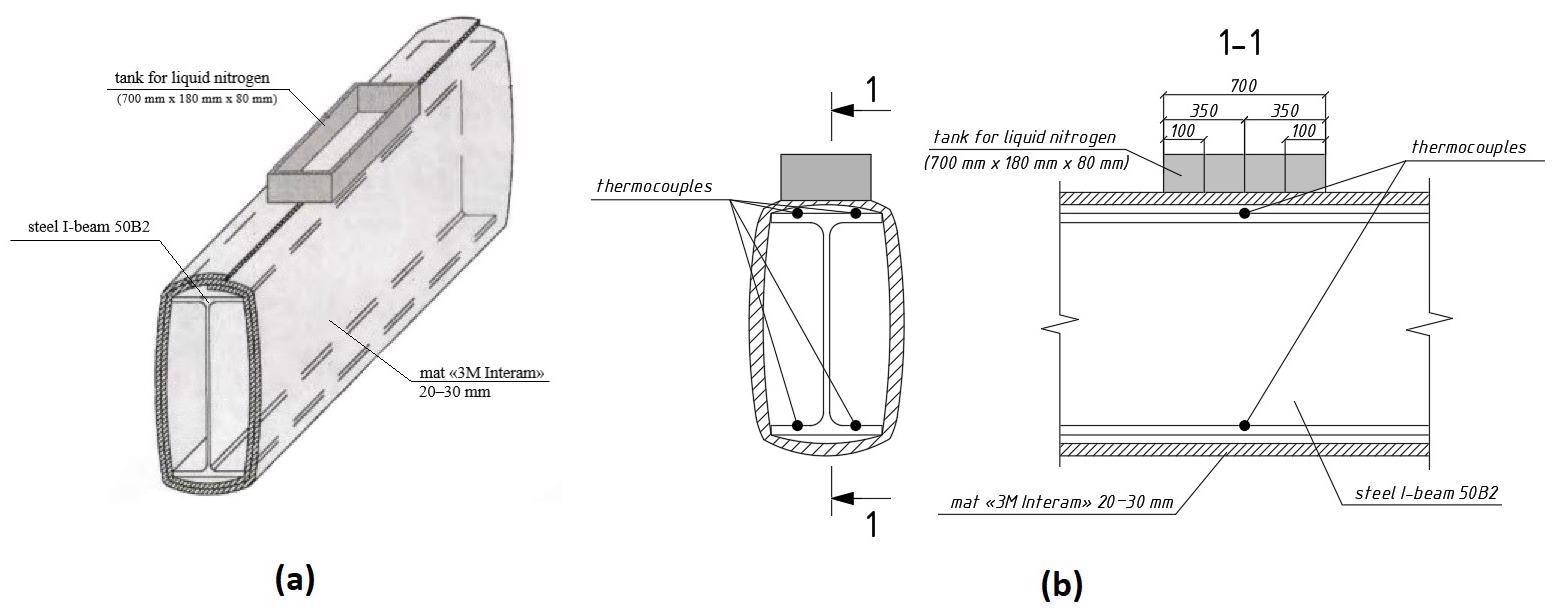
Figure 2. (a) Schematic diagram of the fire protection coating assembly; (b) Section of the fire protection coating assembly with thermocouple location. Image Credit: Gravit and Shabunina, 2021.
A tank of polystyrene foam and sealant residues were eliminated from the surface after the exposure to liquid nitrogen on the flame retardant systems of samples No. 3.1 and No. 3.2. The samples were later placed in a test furnace, in which a hydrocarbon temperature regime was retained.
Results
The Results of Experiment No. 1
The observations showed that sample No. 1 of 50 mm thickness offers fire protection efficiency, and no visible changes were found in the external state of the sample (Figure 3). After 95 minutes—upon attaining the critical temperature on the sample—the experiment was stopped.
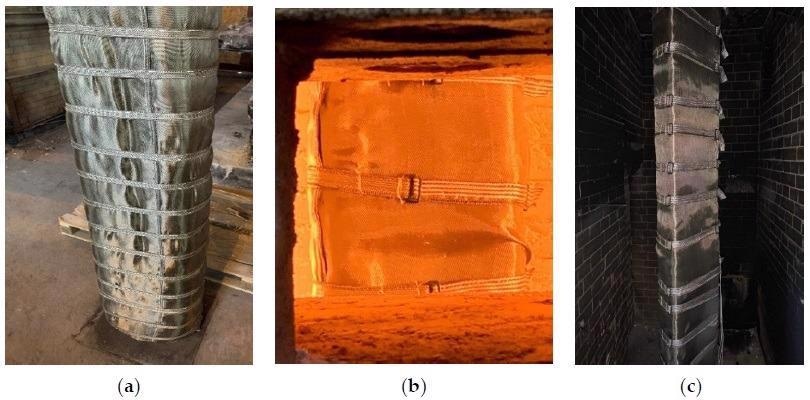
Figure 3. (a) Sample No. 1 before the test; (b) during the test; (c) after the test. Image Credit: Gravit and Shabunina, 2021.
The Results of Experiment No. 2
The results demonstrated that sample No. 2 of 20 mm thickness offers fire protection efficiency. The surface showed burning of aluminum foil and slight embrittlement at the end of the experiment. After 92 minutes the experiment was halted after attaining the critical temperature on the sample.
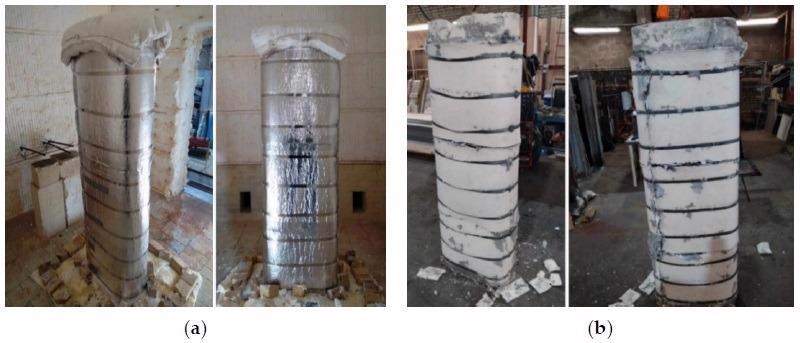
Figure 4. (a) Sample No. 2 before the test; (b) after the test. Image Credit: Gravit and Shabunina, 2021.
The Results of Experiment No. 3
Cryogenic test on the flame retardant systems of samples No. 3.1 and No. 3.2 revealed that 1-hour exposure to liquid nitrogen does not substantially decrease the surface temperature of the protected metal.
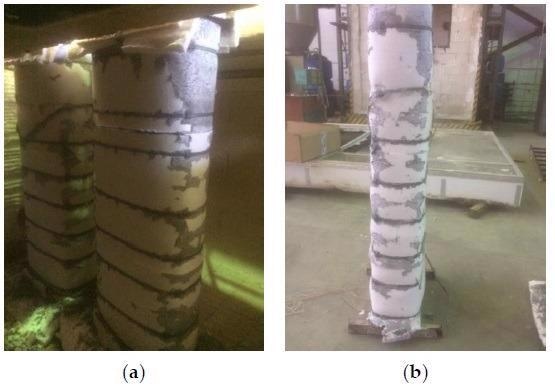
Figure 5. (a) Samples No. 3.1 and No. 3.2 during fire tests; (b) after all tests. Image Credit: Gravit and Shabunina, 2021.
Discussion
Sample No. 3. after cryogenic testing for 60 minutes offers similar fire protection efficacy as the coating of sample No. 1 and sample No. 2, subject to conditions of the hydrocarbon burning regime without cryogenic influence (Table 2).
Parameters/Names of Flame Retardant Coatings |
Sample No. 1 |
Sample No. 2 |
Sample No. 3.1/ Sample No. 3.2 |
Tested samples |
I-section column No.20B1 |
I-section column No.50B2 |
I-section column No.50B2 |
Ap/V, mm–1 |
294 |
172 |
170 |
Thickness of dry layer of fire retardant, mm |
50 |
20 |
20.6/30.9 |
Presence of cryogenic test |
no |
no |
yes |
Cryogenic test time, min |
- |
- |
60 (without reaching critical temperature) |
Moment of the start of the fire test |
as the sample is ready and the furnace is prepared |
as the sample is ready and the furnace is prepared |
2.5 h after cryogenic test |
Fire regime |
hydrocarbon |
hydrocarbon |
hydrocarbon |
Fire protection efficiency |
90 |
90 |
90/147 |
Table 2. Comparison of initial data and obtained results of fire retardant coatings based on STBF. Source: Gravit and Shabunina, 2021.
Figure 6 depicts the temperature changes on the samples at the time of the fire test.
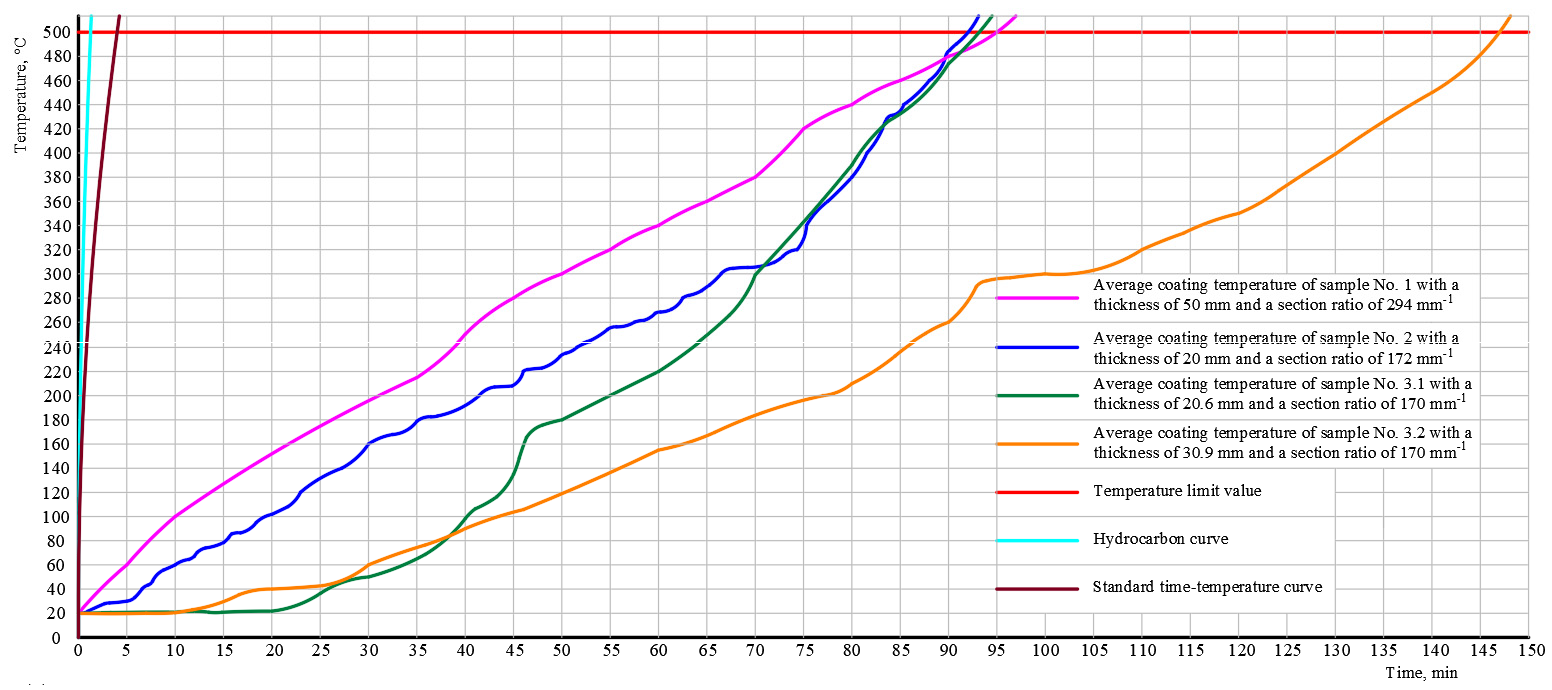
Figure 6. Temperature changes on the samples during the fire test. Image Credit: Gravit and Shabunina, 2021.
Figure 7 depicts a multifactor analysis of the flame retardants as a function of operational, technological, and cost parameters, and puts forth these dependencies as histograms.
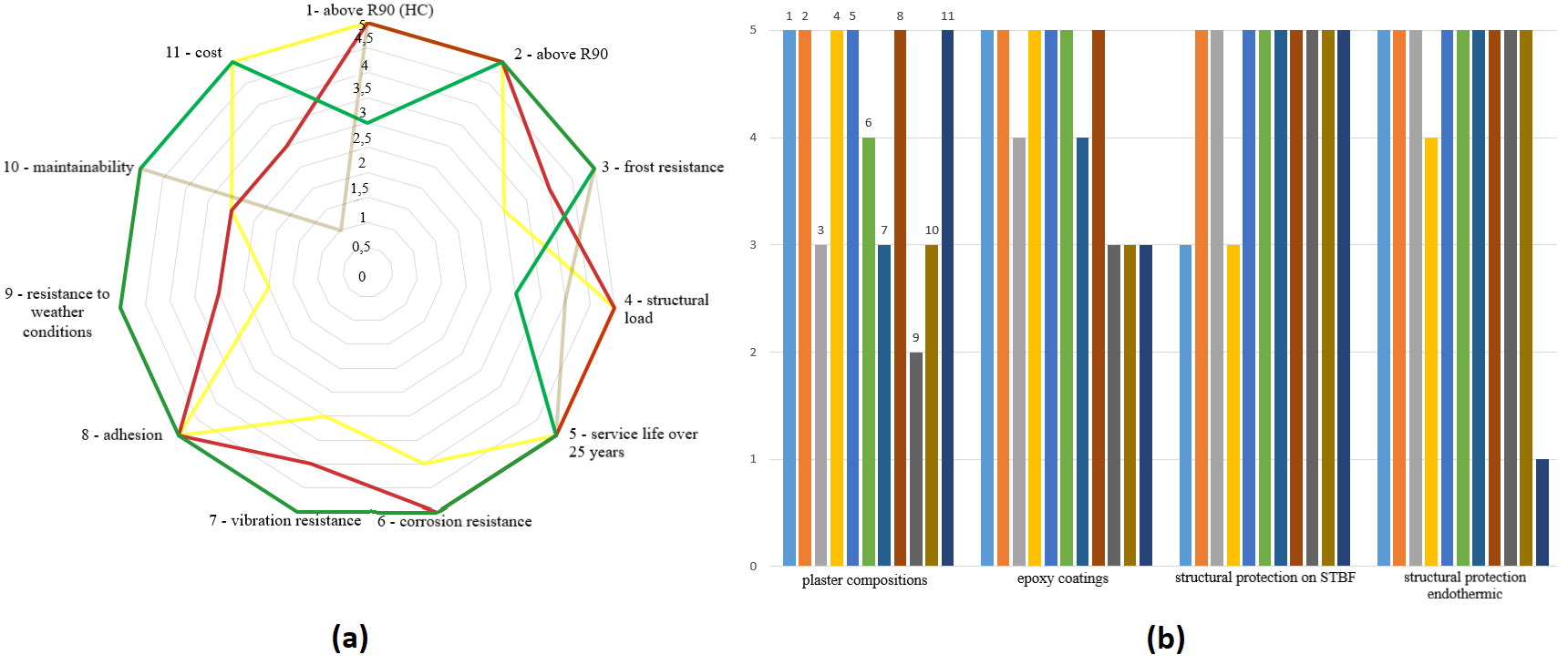
Figure 7. (a) Diagram and (b) histograms for different types of fire protection (red—epoxy coatings, green—structural protection on STBF, yellow—plaster compositions, and gray—structural protection endothermic). Image Credit: Gravit and Shabunina, 2021.
Conclusion
Over the past five years, the design of steel structures with increased fire resistance limits is controlled by international and industry standards of oil and gas facilities.
The results attained from the research shows that the most effective means of fire protection of steel structures in the Arctic and Antarctic are materials based on STBF, offering a “dry” method of installation, long operating time in severe conditions, resistance to the cryogenic spillage of liquefied hydrocarbons and a hydrocarbon fire regime.
Journal Reference
Gravit, M & Shabunina, D (2021) Structural Fire Protection of Steel Structures in Arctic Conditions. Buildings, 11(11), p. 499. Available at: https://www.mdpi.com/2075-5309/11/11/499/htm.
References and Further Reading
- ACIA (2005) Arctic Climate Impact Assessment. Cambridge University Press: Cambridge, UK, p. 1072.
- Gravit, M., et al. (2021) Fire Protective Glass Fiber Reinforced Concrete Plates for Steel Structures under Different Types of Fire Exposure. Buildings, 11, p. 187. doi.org/10.3390/buildings11050187.
- Kim, J. H., et al. (2021) Numerical Investigation of Residual Strength of Steel Stiffened Panel Exposed to Hydrocarbon Fire. Journal of Ocean Engineering and Technology. 35, pp. 203–215. doi.org/10.26748/KSOE.2021.008.
- Imran, M., et al. (2017) Hazard Assessment Studies on Hydrocarbon Fire and Blast: An Overview. Advanced Science Letters, 23, pp. 1243–1247. doi.org/10.1166/asl.2017.8349.
- ISO 20088-1:2016. Determination of the Resistance to Cryogenic Spillage of Insulation Materials—Part 1: Liquid Phase. Available at: https://www.iso.org/ru/standard/67009.html (Accessed on 21st August, 2021).
- ISO 20088-2:2020. Determination of the Resistance to Cryogenic Spill of Insulation Materials—Part 2: Vapour Exposure. Available at: https://www.iso.org/ru/standard/67010.html (Accessed on 21st August, 2021).
- ISO 20088-3:2018. Determination of the Resistance to Cryogenic Spillage of Insulation Materials—Part 3: Jet Release. Available at: https://www.iso.org/ru/standard/67011.html (Accessed on 21st August, 2021).
- UL 1709. Rapid Rise Fire Tests of Protection Materials for Structural Steel. Available at: http://nd.gostinfo.ru/print.aspx?control=27&id=4546871&print=yes (Accessed on 24th August, 2021).
- Russian Government Standard GOST 1363-2-2014. Fire Resistance Tests. Available at: https://www.russiangost.com/p-140694-gost-r-en-1363-2-2014.aspx, Alternative and Additional Procedures. (Accessed on 8th August, 2021).
- EN 1363-2:1999. Fire Resistance Tests—Part 2: Alternative and Additional Procedures. Available at: https://nd.gostinfo.ru/document/6239985.aspx (Accessed on 10th August, 2021).
- Gravit, M (2020) Modeling and standardization of flame retardants for hydrocarbon fire regime. Industrial Coatings. Available at: https://www.lkmportal.com/articles/modelirovanie-i-standartizaciya-sredstv-ognezashchity-dlya-uglevodorodnogo-rezhima-pozhara (Accessed on 15th August, 2021).
- Reid, M (2020) The Piper Alpha Disaster: A Personal Perspective with Transferrable Lessons on the Long-Term Moral Impact of Safety Failures. American Chemical Society, 27, pp. 88–95. doi.org/10.1021/acs.chas.9b00022.
- Zybina, O & Gravit, M (2020) Intumescent Coatings for Fire Protection of Building Structures and Materials. Springer Series on Polymer and Composite Materials. Springer International Publishing: New York, NY, USA. Volume XI, p. 210. ISBN 978-3-030-59422-0.
- McClain, C. R., et al. (2019) Persistent and substantial impacts of the Deepwater Horizon oil spill on deep-sea megafauna. Royal Society Open Science, 6, pp. 1–9. doi.org/10.1098/rsos.191164.
- Evangelista, H., et al. (2013) Preliminary Investigation on the Atmospheric Dispersion of Pollutants Due to Ferraz Fire. INCT-APA Annual Activity Report, pp. 35–42.
- Hassel, M., et al. (2017) Allision risk analysis of offshore petroleum installations on the Norwegian Continental Shelf—an empirical study of vessel traffic patterns. WMU Journal of Maritime Affairs, 16, pp. 175–195. doi.org/10.1007/s13437-016-0123-7.
- Li, J & Hao, H (2017) Internal and external pressure prediction of vented gas explosion in large rooms by using analytical and CFD methods. Journal of Loss Prevention in the Process Industries, 49, pp. 367–381. doi.org/10.1016/j.jlp.2017.08.002.
- Abramov, I., et al. (2018) Increase in the Fire Resistance Limits of Ship and Building Structures with Hydro-Carbon Fire. GAS Industry; (Gazovaya promyshlennost’). No 5, pp. 108–117. (In Russian). Available at: https://neftegas.info/ (Accessed on 15th August, 2021).
- Fireproofing for Hydrocarbon Fire Exposures // GAPS Guidelines. (2000) Publication of Global Asset Protection Services LLC. Available at: https://www.appliedbuildingtech.com/system/files/gap2.5.1.fireproofingforhydrocarbonexposures.pdf (Accessed on 24th August, 2021).
- Palazzi, E & Fabiano, B (2012) Analytical modelling of hydrocarbon pool fires: Conservative evaluation of flame temperature and thermal power. Process Safety and Environmental Protection, 90, pp. 121–128. doi.org/10.1016/j.psep.2011.06.009.
- Cirpici, K. B., et al. (2016) An analytical approach for predicting expansion of intumescent coating with different heating conditions. In: Proceedings of the 12th International Congress on Advances in Civil Engineering, Istanbul, Turkey, pp. 1–8.
- Hiroya, Y., et al. (2019) Simplified Method to Define the Cryogenic Spill Hazard in LNG Liquefaction Facility. Chemical Engineering Transactions, 77, pp. 505–510. doi.org/10.3303/CET1977085.
- Hiroya, Y., et al. (2016) Optimization of cryogenic spill protection insulation thickness. Chemical Engineering Transactions, 48, pp. 643–648.
- Mikalsen, R. F., et al. (2019) Jet fires and cryogenic spills: How to document extreme industrial incidents. In: Proceedings of the Sixth Magdeburg Fire and Explosion Days conference proceedings, Magdeburg, Germany, pp. 1–6.
- UL 263. Fire Tests of Building Construction and Materials. Available at: https://standardscatalog.ul.com/ProductDetail.aspx?productId=UL263 (Accessed on 24th August, 2021).
- UL 1724. Investigation for Fire Tests for Electrical Circuit Protective Systems. Available at: https://standards.globalspec.com/std/260679/UL%201724%20OUTLINE (Accessed on 24th August, 2021).
- Akaa, O., et al. (2017) Optimising design decision-making for steel structures in fire using a hybrid analysis technique. Fire Safety Journal, 91, pp. 532–541. doi.org/10.1016/j.firesaf.2017.03.018.
- Eremina, T & Korolchenko, D (2020) Fire Protection of Building Constructions with the Use of Fire-Retardant Intumescent Compositions. Buildings, 10, p. 185. doi.org/10.3390/buildings10100185.
- Oliveira, R. B. R., et al. (2017) Intumescent paint as fire protection coating. Revista IBRACON de Estruturas e Materiais, 10, pp. 220–231. doi.org/10.1590/S1983-41952017000100010.
- Gravit, M.V., et al. (2018) Fire protective dry plaster composition for structures in hydrocarbon fire. Magazine of Civil Engineering, 3.
- Rivera, M. M., et al. (2020) A study on the use of PFP in off-shore topside structures subject to localised fires. In: Proceedings of the 28th International Congress on Waterborne Transportation, Shipbuilding and Offshore Constructions, Rio de Janeiro, Brazil.
- Park, D. K., et al. (2021) Effects of the structural strength of fire protection insulation systems in offshore installations. International Journal of Naval Architecture and Ocean Engineering, 13, pp. 493–510. doi.org/10.1016/j.ijnaoe.2021.06.001.
- Kremnev, V., et al. (2018) Energy Saving in Construction by Wide Application of High-Quality Insulation Based on Basalt Fibers. Journal of Modern Physics, 9, pp. 1724–1734. doi.org/10.4236/jmp.2018.99108.
- Russian Federal Law No. 123-FZ. Technical Regulation of Fire Safety. Available at: http://www.consultant.ru/document/cons_doc_LAW_78699/ (Accessed on 25th August, 2021).
- ISO 834-1:1999. Fire-Resistance Tests—Elements of Building Construction—Part 1: General Requirements. Available at: https://www.iso.org/standard/2576.html (Accessed on 24th August, 2021).
- Russian Government Standard GOST 53295–2009. Fire Retardant Compositions for Steel Constructions. General Requirement. Method for Determining Fire Retardant Efficiency. Available at: https://www.russiangost.com/p-21424-gost-r-53295-2009.aspx (Accessed on 28th August, 2021).
- Russian Government Standard GOST 57837-2017. Hot-Rolled Steel I-Beams with Parallel Edges of Flanges. Specifications. Available at: https://www.russiangost.com/p-288806-gost-r-57837-2017.aspx (Accessed on 28th August 2021).
- Eurocode 3: Design of Steel Structures—Part 1–2: General Rules Structural Fire Design. Available at: https://www.phd.eng.br/wp-content/uploads/2015/12/en.1993.1.2.2005.pdf (Accessed on 10th September 2021).