While Industry 4.0 continues to revolutionize the way manufacturing and processing plants operate, many businesses are also looking at how the design and build of a facility can be accomplished more efficiently. Here, Dave Friar, international operations director at engineering solutions provider Boulting Group, explores the concept of modularization and how it is transforming the design and build process both at home and overseas.
Modularization is not a new concept. In fact, many plants have been using it to reduce the complexity of internal systems for many years. However, more and more plant managers are now exploring the model as a way of reducing construction costs of a plant and, more interestingly, testing new markets.
The process involves manufacturing prebuilt components at one site, then shipping them all to the build site and assembling them. Each facility is made up of various container modules of differing sizes, within which all of the required equipment is installed.
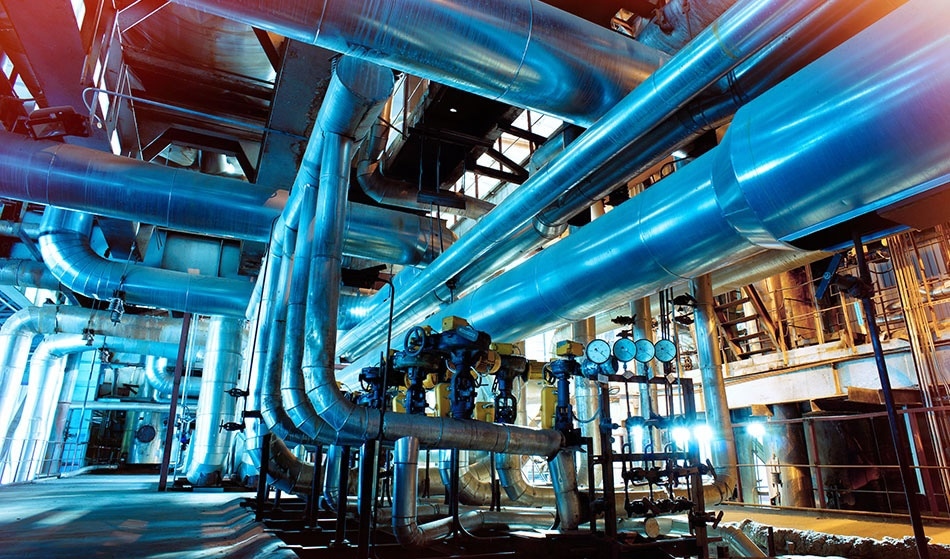
Image credit: nostal6ie/Shutterstock
Drivers for Modularization
By designing and manufacturing all of the components off-site accurate use of materials, a controlled waste system and scheduled delivery can all be ensured. This means the outcome is often more sustainable and cost effective, allowing the delivery of increasingly complex projects.
With many manufacturers relocating operations to developing countries where costs are lower, plants are often built in remote areas with limited infrastructure such as power, road access and construction equipment. Many of these countries also have a severe lack of qualified construction personnel, which can have a negative impact on the overall quality of a project.
Constructing on a dedicated fabrication site, such as Boulting’s facility in St Helens, overcomes these issues as the infrastructure is already in place. Skilled laborers are also at hand to build, test and commission a facility before transporting and erecting in its final location, ensuring a quicker and more cost-effective solution.
If the proposed site for the facility is in a hazardous environment or there is the potential for adverse weather then build location can also be an issue. For example, sea-based constructs are subject to unpredictable seas as well as strong offshore winds, which makes these projects prime candidates for a modular approach.
With the UK set to retain its title as a world leader in offshore wind power, there is the potential to expand the country’s capacity by up to five times its current level by 2030. To ensure this capacity is expanded safely and reliably, modularization may be the key.
Construction at sea can be both dangerous and expensive. Modularization minimizes risk and time spent in the hazardous area, allowing the facility to be built and tested in a controlled environment. An example of this is Boulting Group’s recent work at Rampion Wind Farm. The £1.2 million project saw them deliver work on an onshore fabrication site, minimizing time at sea and ensuring the build was delivered on time and within budget.
While it has its benefits, particularly for projects overseas, some builds aren’t ideal for modularization. If site construction is considered routine and a suitably skilled workforce is available, then modularization may not be the best way forward.
Planning Your Modular Build
Every facility is unique and the build process should reflect that. The actual planning of a modular build is not dissimilar to that of a field construction build. It all comes down to the requirements of the client.
The top consideration for any modular build is the size of the plant and the equipment needed. This immediately impacts on the type and total number of containers required, which can in-turn effect shipping and transportation costs.
The modules themselves come in multiple shapes and sizes, each with their own unique features. Mega, large and intermediate modules require special shipping by either sea or rail. Smaller containers, such as truckable, pipe-rack and skid mounted, are easily moved by large road cargo vehicles. Before selecting the best module for the job, engineers should ensure that there is appropriate access to waterways, rails and roads.
At present, Boulting are working on an alcohol blending plant at their St Helens production facility. The plant, which will be shipped by sea to Angola, consists of eleven purpose-built 40ft containers. The plant itself only takes up six containers, with the remaining five being used to ship additional equipment.
This particular facility is being used to test a potential new market. Should it prove to be a success, the modular build will be taken apart and shipped to a new location and replaced by a fixed build.
If the project is overseas, like the one mentioned above, the containers must follow an ISO footprint, which is similar to a traditional shipping container. However, if the project’s end site is in the same country where it is being prefabricated, skid mounting is a more effective technique.
This approach is a popular method for distributing and storing machinery and involves permanently mounting equipment onto the container frame or rails; ensuring equipment is safely transported to its final location.
While there are no specific regulations and legislations surrounding modular builds, projects must still adhere to the legislative requirements of static builds, including Planning, Building Regulations and Good Manufacture Practice.
Modularization is expected to become more widely used in the years to come, as it grows in line with overseas investment. With so many benefits, it’s hard to see why manufacturers wouldn’t explore the concept’s potential.
Whatever the solution, be it modular or fixed, it’s important that the decision is not rushed and all factors are carefully considered, not just the benefits. Working with a leading provider of prefabrication and modularization services, such as Boulting Group, can ensure the right decision is made for your plant in the most efficient way possible.