Recently, a composite Fiber Reinforced Polymer (FRP) pedestrian suspension bridge was built to connect the John D. Tickle Engineering Building, a new five-story state-of-the-art structure measuring 110,000sq ft, to ‘The Hill’ on Neyland Drive at the University of Tennessee, Knoxville.
.jpg)
Figure 1. First Composite Suspension Bridge at the University of Tennessee
FRP – The Logical Material of Choice
The selection of FRP for fabricating this bridge was due to the structure’s urban location nearby the Tennessee River. The material exhibits superior corrosion resistance in all water conditions and high strength-to-weight ratio properties that facilitated the easy transportation and installation of the material without affecting already heavy traffic in that area of the city.
Furthermore, the material required to show high durability as the bridge (Figure 2) is used as a main passage by students, staff and faculty to access the building.
The bridge’s deck portion spans over 120ft and comprises walkways made from Strongwell’s SAFPLANK® interlocking decking system and DURAGRID® 2" T-1700 pultruded grating panels.
The bridge rail posts were fabricated using 2", 4" and 6" EXTREN® square tubes. Strongwell’s 36" EXTREN® DWB® (Double Web Beams) supported the substructure.
.jpg)
Figure 2. Another View of the Composite Suspension Bridge
Strongwell fabricated the materials for the bridge, which was then shipped to the site. Quality Machine and Welding Co. Inc., a structural steel fabricator and erector, performed the on-site installation of the bridge.
The technical data of this application are provided in the following table:
Product: |
Composite Bridge Deck |
Process: |
Pultrusion, Fiberglass Fabrication |
Materials: |
EXTREN® Series 525 fiberglass reinforced polyester; gray color EXTREN® DWB; DURADEK® T-1700 fiberglass reinforced vinyl ester grating; and SAFPLANK® Interlocking Decking System |
Sizes: |
EXTREN® structural shapes: 6", 4" & 2" Square Tube; 10" Wide Flange; 3" Angle; 36" EXTREN® DWB; and 2" DURADEK® T- 1700 |
For: |
John D. Tickle Engineering Building |
User: |
University of Tennessee, Knoxville |
Conclusion
Quality Machine and Welding’s Vice President, Jeffrey Roth Jr. said that the bridge installation was the first experience of the company with FRP and Strongwell’s cooperation and customer service were excellent during the requirement for minimal field modifications.
Roth also noted the weight benefits of FRP as only a lightweight crane was needed to erect even the largest beams. The company was happy with the project results and is now eager to perform such FRP composite installations in the future.
About Strongwell Corporation
Strongwell has been pultruding fiber reinforced polymer composite structural products since 1956. Today, with more than 65 pultrusion machines and 647,000 square feet of manufacturing space in three plant locations, Strongwell has unequaled capacity, versatility and flexibility to meet the needs of its customers and allied partners. All Strongwell pultruded products are made in the USA. Click here to learn how Strongwell’s pultruded products out perform traditional materials.
The company is financially strong, total quality oriented, technically advanced, and customer focused. Strongwell's customers include Fortune 500 industrial and commercial firms, major architectural and engineering firms, leading contractors and distributors, and many other companies - both large and small - in a variety of markets.
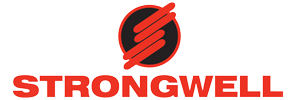
This information has been sourced, reviewed and adapted from materials provided by Strongwell Corporation.
For more information on this source, please visit Strongwell Corporation.