In October 2012, the composites world celebrated a historic milestone in Dawlish, United Kingdom. The world’s first Grade II listed FRP bridge replaced the Grade II listed Dawlish footbridge in the coastal scenic county of Devon.
In the year 1937, the original structure was constructed and was deteriorated beyond repair because of salt spray-induced corrosion along with the harsh marine environment of the region. The replacement of this bridge was a challenge as it was one of the 500,000 man-made structures protected by the UK’s architectural and historic listing.
.jpg)
Solution
Network Rail engineers presented alternative solutions in an attempt to refurbish the corroding girders, roof, protective paintwork and rotting timber decking, but replacement by Pipex px FRP fabrication was concluded to be the ideal solution. The Dawlish footbridge was designed and engineered by Tony Gee and Partners and Optima Projects, with installation completed by Bam Nutall.
Portions of the bridge were prefabricated with Pipex px to ensure quick installation and precise testing performance while ensuring the right replication in design of the original 1930's Grade II listed steel bridge. Strongwell's EXTREN® plate was used for light fixture points and heat deflection, SAFPLATE was used for covering flooring, COMPOSOLITE was used as a main floor structure showcasing its advanced toggle system and kick plates as fascia panels on the roof side. On completion, the 60-foot bridge length weighed in at only one-third of its 15-ton steel counterpart and at the same time was more capable of withstanding a 13-ton load. This is the first composite bridge at a mainline station in the UK and is the second FRP footbridge to ever be installed. It has been designed with a life expectancy of 120 years with no maintenance requirements.
Specifications of the Product
The product offered to Pipex Structural Composites Ltd to be used by Dawlish Railway Station, Network Rail was fiberglass footbridge. It is manufactured with the pultrusion or fiberglass fabrication process. The materials used include SAFPLATE® fiberglass reinforced polyester, fire retardant, grit surface, COMPOSOLITE® fiberglass reinforced polymer building panel system and EXTREN® Series 525 fiberglass reinforced polyester, fire retardant.
About Strongwell Corporation
Strongwell has been pultruding fiber reinforced polymer composite structural products since 1956. Today, with more than 65 pultrusion machines and 647,000 square feet of manufacturing space in three plant locations, Strongwell has unequaled capacity, versatility and flexibility to meet the needs of its customers and allied partners. All Strongwell pultruded products are made in the USA. Click here to learn how Strongwell’s pultruded products out perform traditional materials.
The company is financially strong, total quality oriented, technically advanced, and customer focused. Strongwell's customers include Fortune 500 industrial and commercial firms, major architectural and engineering firms, leading contractors and distributors, and many other companies - both large and small - in a variety of markets.
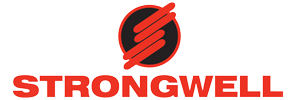
This information has been sourced, reviewed and adapted from materials provided by Strongwell Corporation.
For more information on this source, please visit Strongwell Corporation.