Plywood is made by slicing wood into thin veneers and gluing the veneers together to form a sheet. By alternating the grain direction for successive layers, the sheet has similar areas of grain in the direction of the width of the sheet and the length of the sheet. Therefore, plywood sheets have properties that are nearly the same in both directions in the plane of the sheet, making it ideal as a membrane. By using thin slices of timber in the manufacture of these products, the size and influence of any natural characteristic is limited to the thickness of the veneer. Characteristics • High strength and stiffness to weight ratios - make its handling and installation very cost effective in applications such as residential and commercial flooring, shear-walls and diaphragms, formwork and webbed beams. • Surface dimensional stability - the cross-laminated construction of plywood ensures that sheet sizes remain relatively stable under changes of temperature and moisture, making it particularly suited to formwork applications. • Panel shear - approximately double that of solid timber due to its cross laminated structure, making it suitable for use in gussets for portal frames, webs of fabricated beams and thin plywood bracing panels. • Workability – plywood is easily nailed close to edges, which is important when used with relatively slender timber backing members, or as bracing, webs and gussets in portal frame construction. • Impact resistance – plywood, as with all timber products, has the ability to accommodate the occasional short-term load up to twice the design load. This property is advantageous for applications such as loading docks where vehicle impact can be expected or in buildings subject to seismic activity or cyclonic winds. A variety of plywoods are made with the following variations: • Strength of the material • Thickness of the material • Glues – interior, exterior, marine • Quality of finishes of faces • Species of face and other plies Applications Plywood is made in sheets and can have attractive veneers placed on the face. It is an appropriate product to use as a lining board. Veneers in adjacent sheets can be matched for grain and colour, to make large expanses of uniform timber facing. By using patterns of small holes, acoustic panels can be created. Plywood can also be effectively used as the face of doors, and in cabinetry in buildings. Structural plywood can find uses as nailing gussets in trusses, webs in I-beams or box beams, as well as for bracing in buildings. Thicker sheets can function well as slab elements and are often used in formwork or floors. The following table is a guide to the thicknesses and stress grades required for typical applications: | Lining Panels | 3-15 | N/A | Residential Flooring | 13, 15, 17 | F11, F14 | Industrial flooring | 17-25+ | F11-F22 | Diaphragms | 9-15 | F11, F14 | Bracing (shearwalls) | 3-15 | F11, F14, F27 | Box Beams | 7-12 | F11, F14 | Portal Frame Gussets | 12-25 | F11, F14 | Appearance plywood is specified by the required characteristics of the face veneers – species, colour, grain; and by thickness, lamination pattern, type (durability) of glue bond and any treatment. Structural plywood is specified by thickness, grade, species, type (durability) of glue bond and any treatment. Manufacture Plywood is made by laminating thin sheets of veneer together with the adjoining laminates at right angles to each other. This produces a sheet-like product with grain running in both of the principal directions in the plane of the sheet. 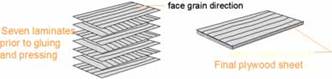 An odd number of laminations is usually used with each veneer laid up at right angles to the previous one. This gives a sheet with just more than 50% of the fibres in the main direction (the face grain direction) and just less than 50% at right angles to that direction as shown. Quality control The Plywood Association of Australia has operated a quality assurance program since 1963. This ensures that the plywood manufactured by mills participating in the scheme conforms to the relevant Australian Standard. Interior Panels Decorative plywoods are frequently used as internal linings and ceilings of dwellings and commercial premises providing the feel and appearance of timber, but with the advantages of a panel product. These interior linings can be made from appearance finish structural plywood, or a decorative internal plywood. In some cases, holes can be used to give the panels appropriate acoustic properties. 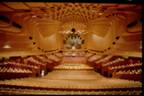 The standard sheets are called Interior Plywoods. A large range of grain patterns and species is available, giving a large variety in decorative appearance products. Because of the cross-grain, the plywood can be significantly thinner than solid timber lining boards, and it is less prone to movement in changing environmental conditions. Clear finishing of all these decorative panels is all that is needed to protect the surface from scuffing and stains. External Cladding A range of preservative treated plywoods is produced for external cladding. This plywood can effectively connect the floor framing to the top plate and can be used as tie-down as well as bracing walls. The sheets must be joined on studs, so careful attention needs to be paid to the framing layout. In order to resist weathering, either a good quality opaque paint is required, or regular replacement of a clear finish. ‘Stucco’ or other render systems will also protect the plywood. 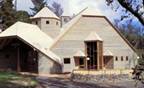 Plywood Sheets – Flooring Plywood flooring enables large areas to be covered quickly and economically. It’s inherent dimensional stability also means that it is suited to the ‘platform’ construction method where it can withstand the rigours of bad weather that may be encountered when the floor is installed in advance of the wall and roof framing. These same properties also make it suitable for small increases in moisture content if used in ‘wet’ areas such as laundries and bathrooms enabling the one flooring system to be used throughout the building. In ‘wet’ areas a good quality seal is required over the plywood to protect it from moisture during normal service. This will enhance its durability. Plywood laid on timber joists is effective at reducing floor bounce and vibrations, providing the comfortable feel of a timber floor. The plywood surface can be covered with a wide range of coverings such as carpet, vinyl, cork or ceramic tiles. Bracing (shearwalls) Plywood is particularly suited to applications such as shear or bracing walls that are designed to resist the effects of wind or earthquake that may cause the structure to sway. The cross banded nature of plywood allows close nailing at edges and enables the use of very thin plywoods to achieve a cost effective bracing system. Plywood Webs and Gussets The high shear strength of plywood makes it suitable for bracing panels or as webs in manufactured beams such as plywood webbed I-beams and box beams. Timber flanged plywood webbed box and C-section beams can provide a stable, lightweight and cost effective alternative to conventional timber trusses in applications where headroom is an issue, or where the loads on a beam are relatively light or uniformly distributed, but the span is large. Formwork The timber veneers used in plywood are relatively stable along the grain, and therefore the cross-laminated construction of plywood ensures that sheet sizes remain relatively stable under changes of temperature and moisture. This factor is important in platform floor and concrete formwork construction where exposure to moisture is inevitable. In addition to dimensional stability, plywood’s high strength and stiffness to weight ratio, ease of working and impact resistance are well suited to the formwork application. The ruggedness of the product allows it to tolerate the abuses that often occur on construction sites. The material requires the normal tools that a form worker would use for other timber products, and the sheets can be readily curved or cut to form the unusual shapes required in architectural or civil construction. Formwork timber has high durability glues and is generally coated to improve wear resistance of the faces. Standard Sizes and Thicknesses Plywood is available in several lengths and widths and a wide range of thicknesses. Non-standard panel sizes are available on request from manufacturers. However, the most common plywood panel dimensions (mm) are; Length – 2700, 2400, 1800 Width – 1200, 900 Sheet sizes (mm) for plywoods include: 2400 ´ 1200 2400 ´ 900 2100 ´ 1200 2100 ´ 900 1800 ´ 1200 1800 ´ 900 A 2250 mm length panel is often used for flooring applications, as this size suits the standard floor joist spacing of 450mm. Standard thickness: (mm) Structural – 3, 4, 4.5, 6, 7 12, 13, 15, 17, 19, 21, 25 Marine, exterior and interior – 3, 4, 6, 9, 12, 16, 19, 25 Specifying plywood When specifying plywood, the following information needs to be supplied: • Number of panels • Length ´ width ´ thickness (mm) • Plywood type (eg. structural) and Standard (eg. AS/NZS 2269) • (if structural) Stress grade and ID code • Face and back grades • Glue bond type • PAA product certification stamp • Preservative treatment level Veneer Quality There are 5 veneer qualities specified for plywood in the Australian Standard. The veneer quality relates to appearance only, and not to structural properties. • Veneer Quality A: is a high appearance grade veneer suitable for clear finishing where surface decorative appearance is a primary consideration. • Veneer Quality S: is an appearance grade veneer that permits natural characteristics such as knots as a decorative feature. The type and frequency and type of characteristics permitted is part of a written specification acceptable to both manufacturer and consumer. • Veneer Quality B: is an appearance grade suitable for high quality paint finishing. • Veneer Quality C: is a non-appearance grade with a solid surface (all open defects are filled) and is designed specifically for applications requiring a solid non-decorative surface such as flooring which will be overlaid with a decorative flooring surface. • Veneer Quality D: is a non-appearance grade with open imperfections up to 75mm wide, and is designed for applications such as structural plywood bracing. The plywood veneer quality is specified by two letters; the first being the face veneer quality and the second the back veneer quality. For example, AA for marine plywood, AD for wall cladding where only the front face is visible, CD for structural plywood flooring DD for structural bracing Bond Quality Four types of bond quality are defined in AS2754.1. The appropriate type bond must be matched to the application and service conditions. Type A bond: is a permanent bond, recognisable by its black colour, which will not deteriorate under wet conditions, heat or cold, and is required for all structural and marine plywoods, and in areas around sinks, vanity units and laundry tubs. Type B bond: is appropriate for a maximum of two years exposure for applications such as formwork or for semi-exposed external door skins. Type C bond: is suitable for non-structural interior applications, free from wet or damp conditions. Type D bond: is appropriate for non-structural internal low-humidity environments such as internal panelling. Properties Because plywood is made from thin laminates, the influence of any strength-reducing characteristic can only affect the laminate in which it is located. The others can carry load around a potential weakness in one plywood laminate. Thus the effect of any strength-reducing characteristic on plywood behaviour is much less than the effect of the same characteristic in a piece of sawn timber. Structural properties of plywood tend to have less scatter than those for sawn timber. The characteristic properties are generally higher than the characteristic properties of the materials from which the products were manufactured. The bending strength, tensile strength and compression strength are given mainly by the strength of the laminates that are oriented in the direction parallel to the principle stresses induced by the loading. The fibres running in both of the directions in the plane of the sheet mean that it has high shear strength in the plane of the sheet. Australian structural plywood is graded to an F-grade system with properties given in Table 5.1 of AS1720.1. These properties are different values to the F-grade properties for sawn timber in Table 2.4 of AS1720.1 |