May 11 2007
This article was updated on the 7th February 2019.
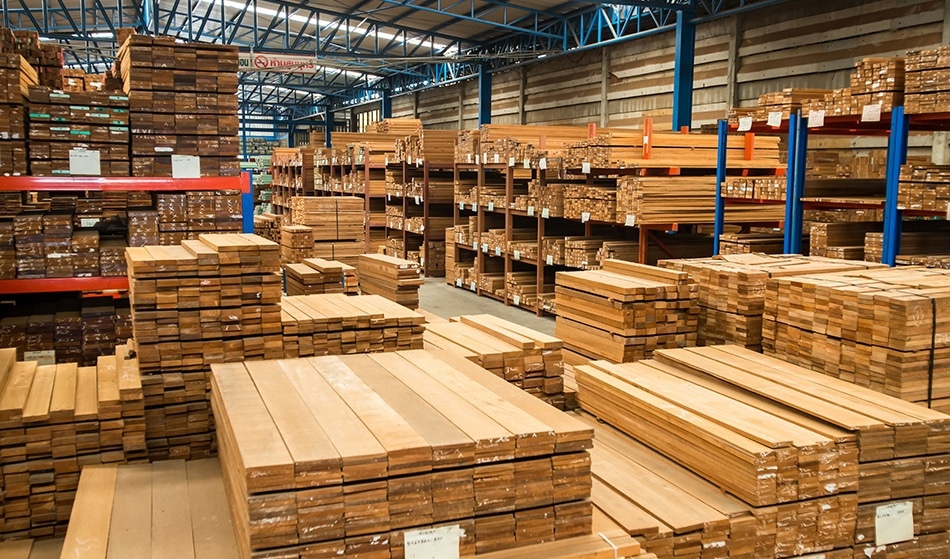
pinyo bonmark/Shutterstock
Seasoned timber has an average moisture content of 15 percent (although moisture readings may occasionally reach 18%), but the bulk of any package of seasoned timber will have a lower moisture content. Most appearance products are seasoned and may have special requirements for moisture contents that are significantly less than 15%. Many structural products are now specified as seasoned.
Seasoning is the process of drying timber to remove the bound moisture contained in walls of wood cells, producing a new product called "seasoned timber." Seasoning can be achieved in a number of ways, but all methods aim to remove water at a uniform rate to prevent damage to the wood during drying (seasoning degrade).
Seasoned timber has better superior dimensional stability than unseasoned timber. Moreover, it is much less prone to warping and splitting during service. In higher grades of timber, especially hardwoods, the seasoning process could enhance the basic characteristic properties of timber; increasing stiffness, bending strength, and compression strength.
Moisture Content of Wood
Water is stored in wood in two primary forms:
- As free water in the vessels and cells; used to move nutrients within the tree
- As cell or bound water, which is an integral part of the cell walls
Seasoning removes all free water and most bound water in the wood. In the removal of the bound water, the wood cells change in size and shape. Due to this, a part of the process must be carried out with careful control over drying rate.
When the timber is first cut, the initial reduction in moisture content is a result of free water loss. This usually occurs without any significant dimensional changes to the timber as the loss of moisture represents the drainage of pores in the timber. If the environmental conditions are favorable, the moisture loss continues until all free water is released to the atmosphere. This point is known as the fiber saturation point (fsp). The fiber saturation point varies minimally with each piece of timber, but it generally maintains a moisture content of between 25 and 30 percent. The loss of free water will occur relatively quickly in small cross-sections of timber, even if the timber is exposed to rain.
Even when all free water has been lost, the timber will still be classified as unseasoned as its moisture content would still be above 25 percent. Further drying is required to bring the moisture content down. This additional reduction in moisture content, below fiber saturation point, requires a reduction in the amount of bound water in the wood's cell wall, which in turn needs more energy and occurs more slowly than the loss of free water. It also results in a reduction in the size of the cell walls, which causes the timber to shrink in size.
Kiln Seasoning
A number of commercial processes for seasoning of timber are available, but the most common one is kiln-drying. Kiln seasoning accelerates the process of seasoning by using external energy to drive out moisture. The timber is stacked in the same way as it is for air drying, and is placed inside a chamber in which the conditions can be varied to provide the best seasoning results. Air is circulated around the charge (stacked timber), and the temperature and humidity can be varied to provide optimum drying. Each species has different cell characteristics and would, therefore, require different drying schedules. Typically, the timber may be in the kiln for a period of two days to a week.
Generally, it is not feasible to kiln-dry structural timber in thicknesses greater than 45 mm, although there are limited amounts of 70 mm thick kiln-dried softwood members in the market place. All untreated structural pine and some commercial hardwoods are seasoned, mostly using kilns that are often heated by sawmill by-products or gas.
Studies are continually being done to determine kiln drying schedules for different species, but researchers were already able to develop a kiln supervisor tool that would be able to analyze kiln productivity and use through a variety of performance indicators [1]. An optimum schedule will remove the moisture as quickly as possible, rendering minimal damage to the dried timber.
After kiln seasoning, there will often be some damage to cells near the surface of the wood. This is because all of the moisture passes through those cells; however, they could easily be “pumped back up” in a reconditioning chamber. This chamber introduces steam and puts some moisture back into the outer cells, ultimately removing the effect of seasoning collapse.
While kiln-seasoning of softwoods such as pine species is generally a relatively quick process, seasoning of hardwoods tends to be a much longer process. This is mainly due to the different (closed) cell structure of hardwoods.
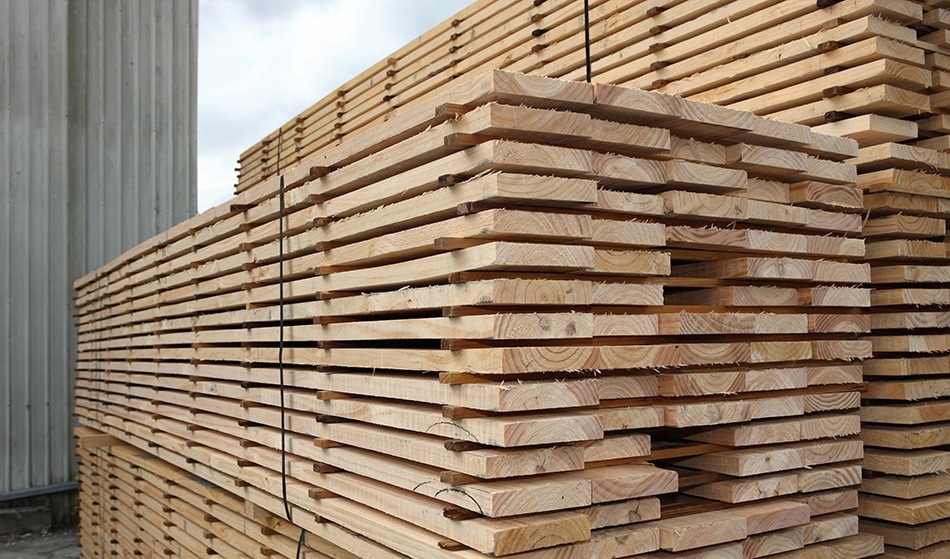
Joe Gough/Shutterstock
Plantation softwoods seasoning in Australia mainly utilizes “high temperature” drying, where the kiln temperature is significantly higher than the boiling point. This higher temperature permits the softening of lignin in the timber, which begins to occur at about 90°C. The softened lignin allows the timber fibers to realign themselves while the stack of timber is being held straight by weights. The tendency to twist and distort during the drying process may be avoided, producing timber will remain straight when cooling under restraint. A typical drying process for plantation softwoods using this principle involves pre-steaming for 4 hours and drying at temperatures of about 115°C until the moisture content falls below 10% This step will typically take 3 to 5 days. The timber is then humidified with steam for about 4 hours and cooled under restraint.
Conventional kiln-drying for hardwoods uses temperatures below the boiling point of water. This avoids damage to the wood fibers which, if the seasoning is not adequately controlled, can experience loss of strength. In seasoning hardwoods, the process is slow and can be economically undertaken first. Another option would be to partially season the hardwoods for a period of three to nine months, depending on the thickness of material, the ambient temperature and humidity, and the species. The partial seasoning process can be accelerated for some hardwoods by using fan-forced pre-drying in a controlled environment. This reduces the lead time for kiln-drying to 20 to 30 days.
Once the sawn hardwood material reaches fiber saturation point or moisture content of about 20 to 25 percent, the material would then be placed in kilns between 10 to 14 days (depending upon the thickness of the sawn timber), so that moisture content falls below 10 to 15 percent. This drying process must strictly be controlled or monitored to avoid drying degrade.
Air Drying
The traditional method of seasoning timber was to stack it in the air and let atmospheric heat and the natural air movement remove the moisture. The process has undergone a number of refinements over the years that have made it more efficient. It also reduced the quantity of wood that was damaged by drying too quickly near the ends in air seasoning.
The basic principle is to stack the timber so that plenty of air can circulate around each piece. The timber is stacked with wide spaces between each piece horizontally, and with strips of wood between each layer to ensure that there is also a vertical separation. Air can then circulate around and through the stack, to slowly remove moisture. In some cases, weights can be placed on top of the stacks to prevent the warping of the timber as it dries.
Air-drying is a relatively slow process, particularly for hardwoods, typically taking six to nine months to reach a moisture content in the range at a fiber saturation point. The time taken for air-drying is a function of the thickness of the timber.
While little additional energy needs to be supplied for this type of seasoning, there are still disadvantages. For instance, the stacks of timber require a lot of land, the process may lead to a potential fire hazard, and the product is not able to be sold for a considerable time. The interest costs on holding the stock for long periods may also be significant. In timber air-drying, the amount of drying is very much governed by the relative humidity of the drying environment and will often vary within individual boards as well as within the stack itself.
Solar Drying
Solar seasoning offers a compromise between the low energy requirement of air drying and the speed of kiln drying. A number of different configurations have been tried, including a double skinned inflatable kiln. Because the energy input is variable, the kilns often have effective insulation to hold the heat inside at night time. Some kilns developed overseas could generate temperatures of over 40oC inside even when the external temperature is -20oC.
Solar-drying, which can take nearly twice the time required for kiln-drying, is well suited to high-grade applications such as furniture. It is a slower and gentler form of kiln drying. Some seasoned hardwood producers use air-drying down to fiber saturation point (FSP) before stacking the timber in the solar kiln. Research has found evidence that solar drying, particularly using timber solar dryers, significantly reduce drying time and drying defects compared to air dryers [2].
Microwave Seasoning
Microwave seasoning is an uncommon method of removing moisture but may serve as a complementary tool to air dryers to facilitate faster and higher quality wood drying [3]. It is an established technology in Canada that is now used for drying some commercial sizes of North American softwood timber.
In this method, pulsed microwave energy is directed into layers of timber in a manner that will drive the moisture out of the timber at rates that will not cause the seasoning to degrade. The process can deliver energy that varies from second to second to suit the moisture content of the timber at the time, as well as the ambient conditions.
In some cases, microwave energy delivery can be combined with low ambient pressure to produce optimal seasoning speeds.
Chemical Seasoning
Chemical seasoning is used for high-value applications where the timber is required to be completely free of surface checks (e.g., rifle butts, golf club heads, and carvings). The process involves soaking the green timber (as soon as it is cut) in a hygroscopic chemical for about a day, which slows down the rate of moisture loss and minimizes the risk of inducing the internal stresses which cause checking to occur during the subsequent air-drying.
Seasoning Degrade
All producers aim to minimize the extent of damage that occurs during seasoning. They remove any piece that has degraded significantly during the grading process. Typically, users of timber do not have to worry about seasoning degrade because all affected pieces have been rejected during production. The term “seasoning degrade” can also be used to refer to the population of timber that has been downgraded because of the degradation that occurs during drying.
Seasoning degrade can produce timber that has reduced utility due to the following factors:
- Twisting and other deformations, such as bow and spring. One of the most commonly observed forms of degrading in wide pieces of timber (e.g., boards) is cupping of the member. The board becomes concave on the face further from the corewood (or center of the log) and convex on the other face.
- Cracks that do not extend right through the timber. They often present as a small surface crack that doesn't extend deep into the timber but will reduce the appearance value of the timber and make it more difficult to coat with a surface finish.
- Internal checking – Also known as honeycombing, these checks are not visible on the surface but are exposed when the piece of timber is cut.
- Splitting – These are cracks that extend right through the timber. They are most prevalent at ends.
- Collapse – Some cells collapse, and the surface of the timber will have a corrugated or washboard appearance. The cross-section may be irregular rather than the rectangular shape it started with. Collapse can be recovered in some species through controlled re-humidification in a steaming chamber.
- Blackheart – A number of species are prone to severe checking and collapse, in the zone of dark-colored wood in the core material of logs. This can cause problems when this otherwise decorative material is exposed on the face of a piece of timber.
Sources: