Rigid foams made out of foamed polymers like polyurethane find many uses as building materials, but their manufacture and end-of-life considerations make them a wholly unsuitable product for the sustainable construction industry that the planet needs. Today, a new breed of plant-based rigid foam products has entered the market, allowing developers to make use of the desirable characteristics of rigid foam without the environmental downsides.
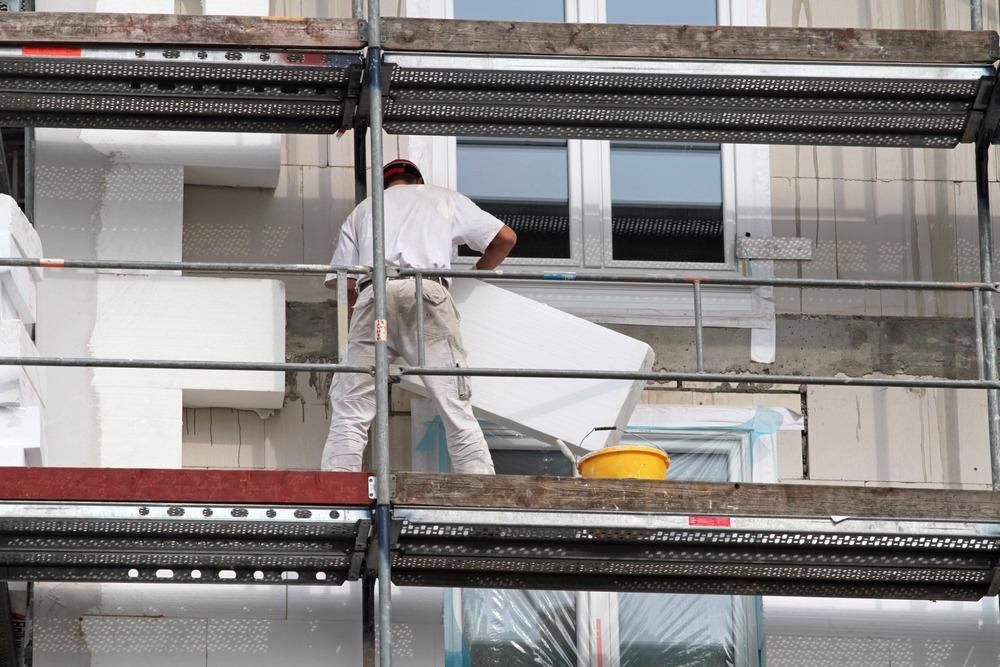
Image Credit: Canetti/Shutterstock.com
About a quarter of the global foam market consists of rigid foams (with flexible foams and semirigid integral skin foams taking up most of the remaining market share). Overall, the foam market is growing at about 7% annually, and is estimated at approximately $82 million worldwide today. Most rigid foam consumers are in the construction industry, where the materials find diverse applications in sealing, thermal barriers, and flooring.
Rigid foams made out of polymers like polyurethane became so common in the construction industry due to their easy formulation and processing, and relatively low energy use for manufacturing. Other polymers used in rigid foams include polyethylene, polypropylene, and polyacrylonitrile butadiene styrene (polystyrene). All of these plastics are made out of petrochemicals found in oil and are very difficult to dispose of.
For these reasons, there has been considerable interest in recent years in developing plant-based polymers that can be foamed into rigid materials for the construction industry.
A new generation of rigid foams made out of biopolymers is currently growing in terms of market share. These foams are made from biopolymers like ethylene vinyl alcohol, polyvinyl alcohol, polysaccharide, and starch. Biopolymers typically represent less embodied carbon (CO2e) than regular, fossil-fuel-based polymers. This is not only because it is less energy-intensive to extract biological, plant-based polymer sources than it is to extract oil and gas, but also because of the CO2 that plants naturally sequester out of the atmosphere while they are growing.
The most common biological sources for rigid polymeric foams are functionalized reactants based on vegetable oil. These reactants are less potentially harmful than petrochemical-based polymers, and can also produce polymers that will biodegrade much more quickly and healthily than fossil fuel plastic does. Significantly, they also come from a renewable source that is usually native to where the vegetable is produced, growing abundantly.
Biofoams are even more environmentally friendly when they are produced with as many biodegradable components as possible. Rigid foam products typically take up large amounts of landfill space or have to undergo costly processing to be destroyed or recycled. But using carefully selected biological ingredients for these products instead means that entire panels can be composted or even used in biomass to energy (BE) power generators.
Commercial applications for plant-based rigid foams use extra reinforcement and additives in the mixture to create multifunctional products. Often, these additives are plant-based themselves. Biofoam manufacturers use additives to increase products’ moisture resistance, fire retarding properties, and ultraviolet protection.
More Materials - Slate: Applications and Advantages
Despite the many advantages of plant-based rigid foams, they still make up much less of the market than the alternatives derived from fossil fuels. Some researchers working closely on this issue lay the blame for this at the feet of manufacturers and developers who are too cautious to make the investments – and long-term commitments – required for biofoams to reach the necessary economies of scale for widespread adoption.
Because of this, increasing the availability of government-funded biodegradability incentives, tax credits, and carbon credits for biofoams will be needed for the rigid foam sector to make a switch. This impetus for industry should correlate with more academic studies on the structural and other properties of plant-based rigid foams.
Understanding the Applications for Plant-Based Rigid Foams in Construction
The main construction industry applications for rigid biofoams are in noise abatement and shock absorption, but plant-based polymers can be foamed for any task that their fossil-fuel-based counterparts can also perform. The original purpose of lightweight foams was to be used as core panels in sandwich composites.
High-density (low flexibility) rigid foams have been made using polyols derived from tall oil fatty acids (from conifer trees). These foams perform well as thermally conductive structural components in a building, providing insulation as well as load-bearing for the building’s design.
A team of researchers working at the University of Latvia, Riga Technical University, and the Latvian State Institute of Wood Chemistry in Riga, Latvia, recently showed that plant-based rigid foam made out of tall oil fatty acids performs comparably to polyurethane rigid foam, suggesting that the material would serve well as a structural thermal break. The research was published in Construction and Building Materials in 2020.
Academic research is also making palm oil a viable candidate for polymerization and foaming into rigid foam products. In a recent conference paper, researchers from Malaysia used scanning electron microscopy (SEM) to show that these products have good dimensional stability at temperature extremes of -150 °C to 700 °C.
References and Further Reading
Ali, E. S., and S. A. Zubir (2016). THE MECHANICAL PROPERTIES OF MEDIUM DENSITY RIGID POLYURETHANE BIOFOAM. MATEC Web of Conferences. Available at: https://doi.org/10.1051/matecconf/20163901009.
Andersons, J., et al. (2020). Bio-based rigid high-density polyurethane foams as a structural thermal break material. Construction and Building Materials. Available at: https://doi.org/10.1016/j.conbuildmat.2020.120471.
Chevali, V., and E. Kandare (2016). Rigid biofoam composites as eco-efficient construction materials. Biopolymers and Biotech Admixtures for Eco-Efficient Construction Materials. Available at: https://doi.org/10.1016/B978-0-08-100214-8.00013-0.
Luo, X., A. Mohanty, and M. Misra (2012). Water-Blown Rigid Biofoams from Soy-Based Biopolyurethane and Microcrystalline Cellulose. Journal of the American Oil Chemistry Society. https://doi.org/10.1007/s11746-012-2100-4.
Disclaimer: The views expressed here are those of the author expressed in their private capacity and do not necessarily represent the views of AZoM.com Limited T/A AZoNetwork the owner and operator of this website. This disclaimer forms part of the Terms and conditions of use of this website.